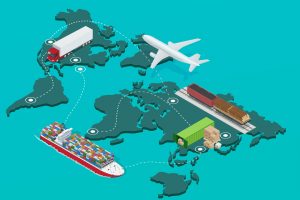
Quando parliamo di
design della propria supply chain esistono due decisioni basilari. La
dislocazione geografica dei magazzini e la tecnologia informatica usata per il coordinamento delle
attività di supply chain. Maggiori sono la complessità dell’offerta e l’ampiezza geografica del mercato e maggiore sarà l’importanza che la tecnologia riveste.
Lo stato dell’arte tecnologico di oggi ci permette di parlare di
modelli di supply chain ‘orchestrati’, dove per orchestrazione s’intende
la sincronizzazione e integrazione di tutte le funzioni di supply chain per far fronte in maniera efficiente e just-in-time alla complessità e alle talvolta drammatiche fluttuazioni della domanda e delle forniture.
Le fluttuazioni sappiamo essere la principale causa di tutte le inefficienze. Chiamate dai professionisti del Lean Thinking “
Mura” (giapponese per “incompatibilità”), queste sono le cause principali delle altre due “M” o inefficienze, “
Muri” (“eccesso” o “sovraccarico”) e “
Muda” (“spreco”).
I sistemi di orchestrazione della
supply chain assolvono a questa funzione:
ottenere efficienza da un sistema complesso, rendendo modulare e coordinabile ogni suo singolo elemento. Le tecnologie informative rendono visibili capacità e carichi di lavoro e tramite la definizione di regole processuali di allocazione aumentano la sincronia, la collaborazione delle parti riducendo buffer di attesa, scorte di emergenza e sovraccarichi di lavoro (“Muda” e “Muri” in gergo lean).
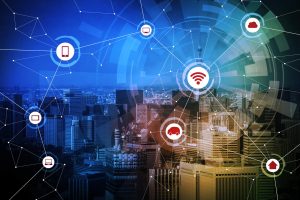
Perché il sistema funzioni, deve
esistere congenitamente slack capacity, o meglio, il sistema non deve operare al 100% della sua capacità. Capacità che deve essere considerata non teoreticamente, ma effettivamente: dobbiamo considerare gli elementi di spreco in un
sistema in cui si sommano lavoro e spreco.
Questo può sembrare un concetto banale ai più, ma
maggiore è il tasso di utilizzazione, maggiore sarà il lead time. È un
effetto di sovraccaricamento naturale che segue una progressione esponenziale, una conseguenza tutta insita al “Muri”. Per evitare l’effetto, il
tasso della domanda deve essere inferiore al tasso di spedizione, per i tecnici il
takt time deve essere inferiore al
cycle time. Questo postulato rende imperativo
conoscere la capacità effettiva del sistema (lavoro e spreco) che deve costituire il livello massimo all’interno del quale l’orchestratore si deve muovere.
Una volta definita l’effettiva capacità del sistema e dei suoi componenti,
l’orchestratore svolge il suo ruolo principale nel gestire le variazioni nella domanda e di ciclo produttivo;
takt time e
cycle time.
La prima regola
per ‘smussare’ il takt time è vendere in funzione delle proprie capacità: sembra banale, ma talvolta la funzione vendita potrebbe non essere facilmente a conoscenza delle effettive capacità produttive. Per risolvere questo problema esistono
soluzioni informatiche come
Oracle Global Order Promising che assolvono a questo compito.
La parte di
domanda che resta comunque variabile (per esempio numerose opzioni e configurazioni di prodotti accrescono la variabilità) può essere
smussata con strumenti di decomposizione degli ordini recepite da un orchestratore che utilizza un sistema di pianificazione centrale per avviare task (ordini di produzione, prelievo, acquisto) dando priorità laddove possano essere recepite con maggiore efficienza, generando quindi costi di change over minimi.
Per affrontare la variabilità nel
cycle time o di lead time le soluzioni restano sempre la
standardizzazione e la digitalizzazione dei processi. La standardizzazione ci consente di visualizzare gli sprechi, le inefficienze, il muda e di eradicarlo con azioni correttive.
La digitalizzazione ci consente di vedere e misurare le inefficienze, di governarle centralmente e di rendere disponibili questi processi ad un orchestratore che ne ottimizza e prioritizza l’utilizzo sulla base della domanda.
Ovviamente la perfezione non è un risultato raggiungibile, ma un percorso da seguire e assorbire.
Ogni variazione rimarrà sempre un’attività di continuo miglioramento che richiederà l’uso di buffer di inefficienza quali magazzini, ore di straordinario, downtime di macchine per change over, ecc. Utilizzare strumenti avanzati come un
orchestratore di processi e attività di supply chain, di pianificazione universale e di calcolo dei lead time come il Global Order Promising permette di far emergere la reale capacità produttiva, ottimizzandone la sua attuale struttura. Questi, insieme con una progressiva standardizzazione e digitalizzazione dei processi, costituiscono i
migliori strumenti per raggiungere l’eccellenza in supply chain contraddistinte da un portafoglio prodotti variegato, ciascuno con differenti opzioni.
Alessandro Evangelisti è Finance & Supply Chain Cloud Evangelist di Oracle Southern Europe