Siccità, Manifattura a secco d’acqua
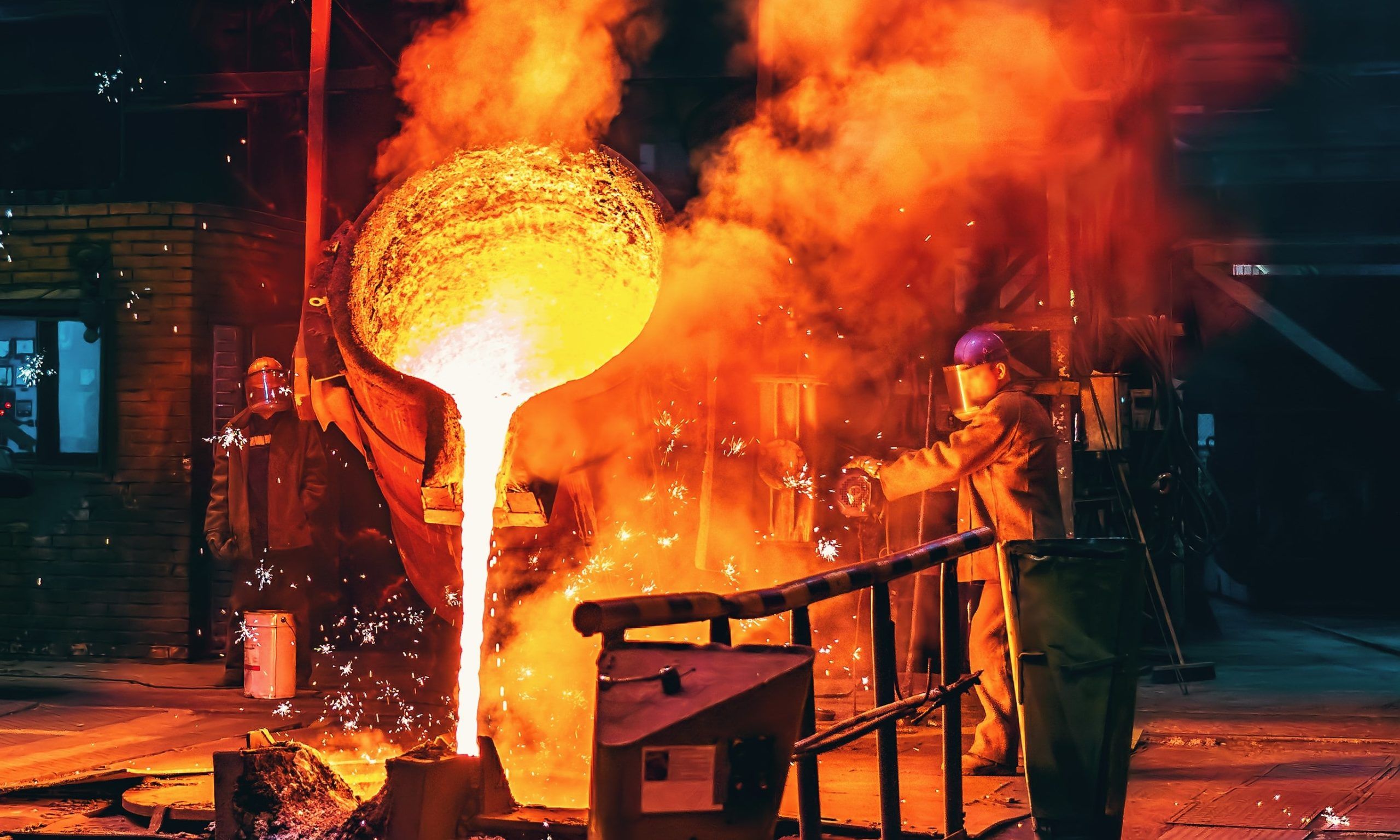
Usare la tecnologia per monitorare il consumo dell’acqua
In accordo con l’adozione di algoritmi intelligenti, si possono infatti prendere in considerazione numerose diverse variabili che caratterizzano le infrastrutture: le dimensioni e l’età del sistema di tubazioni; la disponibilità di acqua pronta per essere trattata; la tipologia e il modello dei contatori installati; le previsioni meteo storiche e future a breve-medio periodo; la cronologia delle misure intraprese per prevenire le perdite d’acqua; le priorità dal punto di vista economico e normativo. L’analisi di queste informazioni può consentire di creare degli schemi anticipatori affidabili per poter individuare a priori i punti di maggiore fragilità della rete idrica. Tonitto 1939, azienda attiva in Italia nella produzione di sorbetto e per i gelati senza zuccheri aggiunti, ha da tempo implementato sistemi di recupero e riutilizzo dell’acqua calda per i processi produttivi che permettono di ridurre i consumi del 50%. Inoltre, ha attivato sistemi di controllo intelligente delle temperature delle celle frigorifere per evitare inefficienze e non disperdere ulteriore energia durante l’intero ciclo produttivo del gelato. “In un momento così particolare della storia, questo impegno diventa indispensabile non solo per la salvaguardia dell’ambiente che ci circonda, ma anche per efficientare e aumentare le potenzialità della nostra azienda. Per questo abbiamo scelto, oltre 20 anni fa, di iniziare un percorso green che ha portato all’installazione di un impianto fotovoltaico, associandolo a interventi sulle linee produttive per evitare gli sprechi, fino al riutilizzo dei materiali presenti all’interno degli uffici”, ha affermato Luca Dovo, Amministratore Delegato di Tonitto 1939.Il caso delle fonderie e del settore siderurgico
Massimo Ansaloni, Direttore Area Tecnica Impianti della Fonderia Ghirlandina, racconta che il vero salto di qualità nella sua azienda è stato fatto quando la tecnologia ha permesso di monitorare e riorganizzare il consumo d’acqua: “Cambiando e modernizzando delle soluzioni tecnologiche in produzione, anni fa abbiamo avviato una sorta di ‘ciclo chiuso’ dell’acqua, per evitarne gli sprechi; abbiamo eliminato poi i sistemi di scambio di calore ad acqua e siamo passati allo scambio ad aria”. Nel settore delle fonderie di seconda fusione (cioè che acquistano ghisa grezza in lingotti, la fondono e la colano in linea di produzione) i processi sono differenti a seconda del tipo di trasformazione della materia. L’acqua, che proviene dalle falde sotterranee e che Ansaloni chiama ‘tecnologica’ per distinguerla da quella sanitaria, cioè da acquedotto, è utilizzata per la sottrazione del calore nei processi di raffreddamento e produzione della ghisa. “Si può costruire un indice di consumo specifico di acqua per tonnellata di ghisa prodotta. Nel nostro caso, il rapporto è rimasto un valore costante degli ultimi tre anni grazie al settaggio svolto con nuovi parametri tecnologici”, ricorda il manager. Insieme con l’acqua, i sistemi di Machine learning permettono di monitorare anche il consumo di elettricità e gas dell’azienda, in ottica di ottimizzazione dei processi. “È probabile, però, che molte fonderie italiane abbiano già fermato la produzione per l’impennata del caro energia e della volatilità del prezzo delle materie prime”, avverte Ansaloni. Secondo una stima effettuata dalla Federazione imprese siderurgiche italiane (Federacciai), infatti, il costo totale delle bollette di gas ed energia elettrica per l’industria manifatturiera italiana nel 2019 è stato pari a 10-11 miliardi di euro; nel 2022, invece, è pari a 60 miliardi di euro. Per Federacciai, ciò implica ben 50 miliardi di extra costi energetici il Manufacturing, di cui la maggior parte è pagata dai settori energivori (cioè acciaio, chimica, carta, ceramica, vetro e fonderie). Questo scenario rende sempre più evidente l’importanza di avere tecnologie adeguate ad affrontare le sfide economiche e produttive.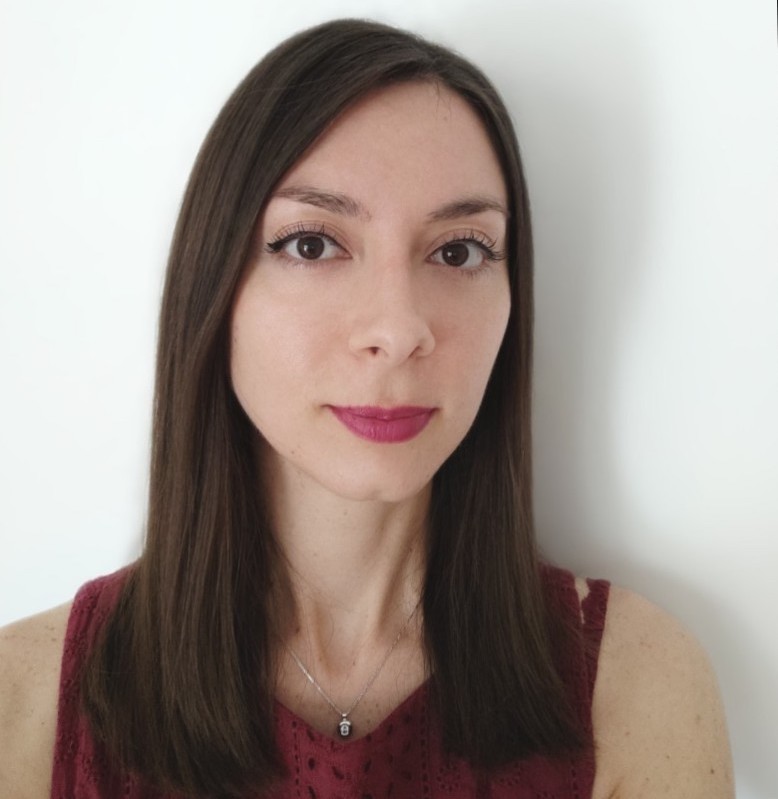
Elisa Marasca è giornalista professionista e consulente di comunicazione. Laureata in Lettere Moderne all’Università di Pisa, ha conseguito il diploma post lauream presso la Scuola di Giornalismo Massimo Baldini dell’Università Luiss e ha poi ottenuto la laurea magistrale in Storia dell’arte presso l’Università di Urbino. Nel suo percorso di giornalista si è occupata prevalentemente di temi ambientali, sociali, artistici e di innovazione tecnologica. Da sempre interessata al mondo della comunicazione digital, lavora anche come copywriter, addetta stampa e social media manager di organizzazioni pubbliche e private nazionali e internazionali, soprattutto in ambito culturale.
fonderia Ghirlandina, green, machine learning, siccità, Tonitto
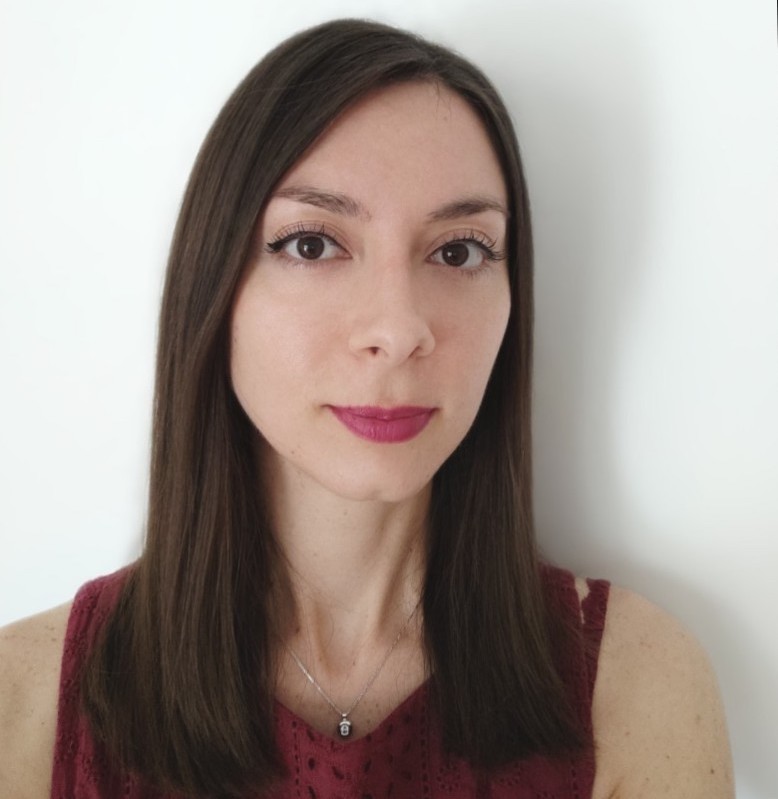