La soluzione PLM implementata da Ansaldo Energia integra progettazione, gestione delle configurazioni, classificazione e configurazione di prodotto e gestione documentale
Ansaldo Energia (AEN) è il principale costruttore italiano di turbine, impianti e centrali termoelettriche. L’attività produttiva dell’azienda si articola in tre linee principali di prodotti: turbine a gas, turbine a vapore e generatori. Per AEN, la gestione del ciclo di vita del prodotto (PLM) è uno strumento essenziale e strategico per la gestione delle informazioni, dei processi e delle risorse finalizzata a supportare il prodotto lungo tutto l’arco di vita, dall’ideazione alla progettazione, dalla costruzione alla vendita, fino alla manutenzione. Per questo motivo, nel corso degli anni AEN ha implementato una soluzione PLM completa che, partita dalla progettazione, si è progressivamente estesa alla gestione delle configurazioni, alla classificazione e configurazione di prodotto e alla gestione documentale, con l’obiettivo di integrare in futuro anche l’impiantistica e il service. Oggi, tutte le applicazioni e le aree operative si appoggiano su una piattaforma unificata, la suite
Teamcenter di Siemens PLM Software, con notevoli benefici in termini di efficienza economica e organizzativa. Su questa piattaforma AEN gestisce infatti i dati CAD 3D con le relative strutture e configurazioni di prodotto, unitamente a meccanismi di gestione delle modifiche e delle configurazioni. Anche i dati CAM sono completamente integrati con i dati di ingegneria, mettendo a disposizione degli addetti nel reparto di produzione tutte le informazioni rilevanti tramite appositi ‘totem’ per la visualizzazione dei dati 2D, 3D, note, dati di produzione ecc.
L’origine del progetto
Stefano Santucci, Business Process Analyst, è la persona che in Ansaldo Energia si occupa di tutto il mondo PLM e dei software e processi a corredo, seguendo le attività di ingegneria di sviluppo, ingegnerizzazione di prodotto, ingegneria di produzione e, infine, ingegneria della manutenzione. “Sono arrivato in azienda insieme a Teamcenter”, racconta Santucci, “che storicamente è stato introdotto nel 1998 come sistema per la gestione della documentazione di macchine e impianti. Successivamente è stato esteso ai materiali e alla struttura di prodotto, per poi introdurre anche la gestione delle modifiche. Dal 2008 è stato avviato un progetto pilota in ambito manufacturing per riorganizzare tutti i processi di fabbrica con l’implementazione di Teamcenter for Manufacturing. In questo modo abbiamo introdotto un sistema per la gestione dei cicli di lavorazione e delle distinte di produzione (MBOM), l’utilizzo di risorse, utensili, attrezzature e
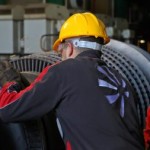
macchine, arrivando fino all’integrazione con il sistema ERP e la pianificazione. Ansaldo Energia ha un parco macchine che comprende apparecchiature a controllo numerico numerose e diversificate, pertanto si richiede una gestione oculata”.
Nel 2008 nasce anche l’ente Ingegneria di Sviluppo, un gruppo di lavoro di 150 persone con il compito di sviluppare nuove macchine (turbine a gas, turbine a vapore e generatori elettrici) e riqualificare i modelli esistenti. La costituzione del nuovo ente risponde a una precisa esigenza, come spiega
Mauro Macciò, Chief Engineer di analisi strutturali. “Fino al 2005 AEN operava sotto il cappello di licenzianti per conto delle quali costruiva sia turbine a gas sia altri tipi di macchine. In seguito alla decisione di non lavorare più su licenza, è nata l’esigenza di creare Centri di Eccellenza per le varie discipline, dediti alla soluzione di problemi di sviluppo e, soprattutto, a raccogliere il feedback del service sul funzionamento delle attrezzature in campo per trasferirlo alla produzione. È stata così creata una struttura che ha riunito diversi enti e personale di Ansaldo Ricerche per svolgere attività su progetti di sviluppo senza coinvolgimento diretto nei problemi di produzione. La caratteristica di questa struttura è la presenza di gruppi che lavorano su un prodotto in maniera trasversale a tutte le discipline, dalla meccanica, all’aerodinamica, all’aria secondaria per il raffreddamento. Sulla scorta dell’esperienza di un’altra azienda del Gruppo, Finmeccanica, e di diverse realtà internazionali, abbiamo riconosciuto la necessità di adottare uno strumento che coinvolgesse tutti i team disciplinari dedicati allo sviluppo, all’approvazione e al rilascio di un prodotto. Da qui è nato il progetto con Teamcenter, che per la sua validità ha ottenuto il premio all’innovazione del
Gruppo Finmeccanica“.
Il progetto con Teamcenter for Simulation
È
Davide Pinna, Innovazione e Sviluppo Prodotti, Ingegneria di Sviluppo, che ha seguito più da vicino questo progetto (battezzato ‘Ingegneria Collaborativa’), con l’inserimento di Teamcenter for Simulation per la gestione dei dati di
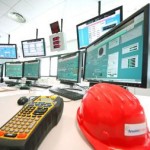
processo nell’area dell’ingegneria di sviluppo. “Il nostro obiettivo era trovare un unico strumento che potesse gestire i dati e i processi di sviluppo e progettazione e consentire un’adeguata ottimizzazione del progetto”, racconta Pinna. “Dopo uno screening accurato basato su un questionario seguito da un test case sulla progettazione termomeccanica di una pala turbina, ci siamo resi conto che non esisteva la soluzione perfetta, bensì prodotti più adatti alla gestione dei dati e del processo, e altri più efficienti per l’ottimizzazione. Ne abbiamo quindi scelto uno per categoria, fra cui Teamcenter per la gestione dei dati e dei macroprocessi”. Per definire questa nuova piattaforma sono stati realizzati tre progetti pilota su componenti reali. L’obiettivo del primo pilota era la gestione dei dati e del processo per il progetto di una pala compressore, un componente di nuova progettazione, con il coinvolgimento delle discipline di aerodinamica e meccanica. Il secondo pilota riguardava un component esistente, con la gestione di un processo di verifica su una pala turbina i cui modelli 3D sono disponibili nel sistema di archiviazione aziendale, dei dati e dei documenti di interscambio tra tutte le discipline coinvolte (in questo caso aerodinamica, scambio termico, sistema di aria secondaria e meccanica); l’obiettivo del secondo pilota era la completa gestione dei dati generati durante il processo di progettazione di una pala di turbina raffreddata.
Infine, il terzo pilota riguardava il progetto di una pala turbina esistente, con il coinvolgimento delle discipline di scambio termico e meccanica e l’obiettivo di mettere a punto un processo di ottimizzazione del sistema di raffreddamento interno della pala. “I progetti pilota si sono conclusi a fine gennaio 2011 con risultati eccellenti”, prosegue Santucci, “a seguire siamo passati alla fase vera e propria di produzione, collegando l’ambiente di lavoro con il resto dell’azienda e gli altri moduli di Teamcenter. In questo modo abbiamo completato tutto il ciclo di vita del prodotto; dopo la prima fase in cui ci siamo concentrati su ingegnerizzazione, sviluppo e manufacturing, abbiamo aggiunto a monte il tassello dell’ideazione e della concezione, e nei prossimi due anni proseguiremo verso valle con manutenzione e service, per chiudere il cerchio e avere un feedback dal campo che ci consentirà di migliorare le attività di ingegnerizzazione e concezione dei prodotti. La piattaforma costruita su Teamcenter diventerà così una fonte di informazioni basilare per chi fa attività di progettazione e potrà validare quanto progettato sulla scorta di dati concreti”.
Benefici misurabili e intangibili
Sono state una ventina le persone coinvolte nei progetti pilota, con grande apprezzamento della soluzione e alti indici di customer satisfaction, grazie al forte coinvolgimento degli operatori nei progetti.
“A favore dell’implementazione ha pesato anche la giovane età media del personale dell’ente Ingegneria di Sviluppo”, aggiunge Mauro Macciò. “Fra gli addetti più anziani, purtroppo, il concetto di ingegneria collaborativa e condivisione del
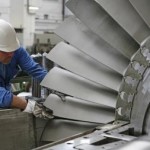
know-how viene vissuto come una minaccia al proprio ruolo in azienda. Naturalmente, abbiamo dovuto fare un grosso lavoro preliminare per svilluppare al nostro interno una cultura del knowledge management. Al di là degli strumenti scelti e prima di avviare qualsiasi processo di informatizzazione, è stato fondamentale formalizzare e strutturare tutta la conoscenza aziendale. In AEN, ad esempio, abbiamo organizzato tutto il know-how in documenti chiamati ‘Design Practice’ che oggi sono archiviati in una cartella protetta in Teamcenter, con possibilità di accesso tracciato e monitorato da parte di tutti gli utenti autorizzati”. Si possono sintetizzare in tre classi principali i benefici ottenuti dall’Ingegneria di Sviluppo di AEN con il progetto
‘Ingegneria Collaborativa’ e il contributo di Teamcenter. In primo luogo, la condivisione del knowhow aziendale, fattore chiave in un’organizzazione in costante crescita e condizione determinante per consentire il rilascio di nuovi prodotti ottimizzati in tempi rapidi. Il secondo punto riguarda la generazione, la gestione e la tracciabilità dei dati. “Poter raccogliere facilmente dati di analisi e report sulle attività svolte garantisce indubbi benefici in termini di tempistiche e certezza del dato, grazie alla possibilità di riutilizzare processi già implementati con risultati documentati e certi”, sottolinea Santucci. Infine, la standardizzazione e l’ottimizzazione dei processi di progettazione, che diventano ufficiali, condivisi e uguali per tutti gli utenti, si traducono in una significativa riduzione dei tempi di lavoro e di calcolo per tutti gli operatori. Sulla base dei progetti pilota e tenendo conto delle diverse tipologie di applicazioni (gestione dei dati, gestione dei
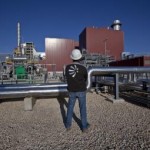
processi e ottimizzazione), i responsabili di AEN hanno stimato una riduzione dei tempi dei processi di progettazione nell’ordine del 10-15%, in linea con le evidenze che si possono ritrovare nella letteratura di settore. “Ciò che l’utente apprezza maggiormente è però il vantaggio intangibile offerto dalla possibilità di visualizzare e revisionare tutti i calcoli svolti in passato, rintracciare ogni processo utilizzato, ogni singolo dato, e riutilizzare eventualmente anche processi di altre persone, con la sicurezza data dal paragone e dal confronto fra diverse soluzioni. Il grande valore operativo di Teamcenter” conclude Macciò, “è la rintracciabilità e la sicurezza del dato, in ingegneria come in produzione, dove è stato implementato Teamcenter for Manufacturing”. È questo, in estrema sintesi, il fulcro di un’implementazione di successo che vede oggi attivi in Ansaldo Energia circa 1.300 utenti Teamcenter e 200 utenti NX.