Lo stabilimento italiano di Lindt vince la sfida della Lean production
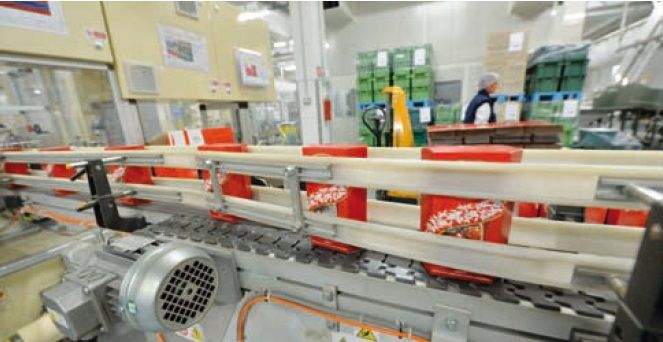
Fabrizio Cerina, Direttore Operations di Lindt, racconta le ragioni, i risultati e i passi fatti per implementare la metodologia Lean in fabbrica
di Luca Bastia
La Lindt di Induno Olona (VA), parte del gruppo svizzero Lindt & Sprüngli, nel giro di pochi anni è riuscita a ridurre notevolmente le spese di produzione, ottenendo un costo del prodotto inferiore a quello di altri stabilimenti del Gruppo. Risultato raggiunto grazie al considerevole impegno nell’introdurre la metodologia Lean o, più precisamente, il TPM, come sottolinea Fabrizio Cerina, Direttore Operations di Lindt Italia, artefice di questo cambiamento che abbiamo incontrato per farci raccontare i risultati e i passi intrapresi per l’implementazione.
Il termine TPM è un acronimo che significa Total Productive Maintenance, e rappresenta una filosofia Giapponese di gestione del manufacturing che risale agli anni 50. Nippon Denso, una società del gruppo Toyota, fu la prima società a introdurre il TPM in tutte le sue fabbriche nel 1960. Lo scopo ultimo è quello di creare una cultura aziendale che ottimizza l’efficienza del sistema produttivo, con una logica di ‘zero incidenti, zero difetti, zero guasti’.
“Abbiamo approcciato la metodologia TPM nel 2010 spinti da fabbisogni sia esterni sia interni – esordisce Cerina –. Quelli esterni consistevano nel fatto che la fabbrica aveva dei volumi in crescita e la prospettiva, che si è poi realizzata, era di avere un forte incremento ulteriore, inoltre cambiava il mix di produzione, cioè si andava verso una maggiore produzione di prodotti confezionati e meno lavorazioni manuali. Non solo, avevamo la pressione per ridurre i costi di produzione soprattutto per quanto riguarda il prodotto più importante di Lindt, ovvero le boules Lindor, pressione che derivava dal fatto che, facendo parte di un gruppo internazionale con poli produttivi messi spesso in concorrenza uno con l’altro, due fabbriche sono stimolate e sfidate a riuscire a produrre la medesima ricetta con un costo del prodotto simile. Questo serve per bilanciare la capacità produttiva in maniera armonizzata a livello globale, perché i Paesi importatori sono molti di più delle fabbriche di Lindt e di conseguenza il Paese che importa cerca di farlo dalla fabbrica che propone il prezzo più basso. In realtà la sfida del gruppo è stata togliere questa possibilità di scelta imponendo un prezzo allineato a quello della fabbrica con costo inferiore: pertanto il rischio per chi non è sufficientemente efficiente è quello di perdere soldi nella vendita ad altre consociate. Noi all’epoca esportavamo e la tendenza era produrre ed esportare sempre di più, ma non riuscivamo a farlo con una struttura di costi competitiva”.
“Anche per quanto riguarda la componente interna avevamo degli indicatori che ci spingevano a un cambiamento – precisa il manager –. Prima di tutto non avevamo una cultura sulla sicurezza sul lavoro molto sviluppata e radicata e avevamo una quarantina di piccoli infortuni all’anno. Ora abbiamo chiuso l’anno con un solo lieve infortunio. Inoltre molte linee avevano bassa efficienza, tra queste anche quelle strategicamente importanti che dovevano produrre le boules Lindor (quella da esportazione, ndr); non avevamo una cultura diffusa della misurazione, non c’erano dei KPIs comuni (il rapporto giornaliero sulla efficienza di un impianto spesso era ‘tutto bene; la linea si è fermata 2 ore’, niente di più); non c’era un training formalizzato, ed essendo noi stagionali e dovendo cambiare la forza lavoro da una linea all’altra a ogni ripartenza molte persone non avevano una conoscenza approfondita delle linee sui cui operavano. In più, dato che la nostra fabbrica produceva e produce più di 800 diversi prodotti, ma le linee non sono altrettante, ogni linea realizzava più di un prodotto, e ogni volta che bisognava cambiare formato nascevano problemi”.
Da qui la decisione di abbracciare il TPM che ha dato risultati estremamente soddisfacenti, con margini di incremento nell’ottica del miglioramento continuo. Certamente l’introduzione di questa metodologia, oltre all’investimento di tempo delle persone coinvolte, ha avuto un costo per i consulenti esterni, ma “posso affermare che l’investimento fatto ha prodotto un ritorno di almeno 20 volte”.
Risultati tangibili e intangibili
“Innanzitutto siamo riusciti ad avere risultati di efficienza superiori allo stabilimento svizzero che produce i nostri stessi prodotti – sottolinea con soddisfazione e orgoglio Cerina – e dunque ora sono loro ad avere un costo superiore al nostro. Abbiamo migliorato la produttività, l’efficienza delle linee e i rendimenti in generale. In maniera costante, negli anni, sono diminuiti i costi, diretti e indiretti; siamo riusciti ad abbassare i consumi energetici e di acqua; sono migliorati i livelli di servizio e si sono ridotti i reclami; dal punto di vista della sicurezza, come accennato precedentemente, c’è stato un netto miglioramento; infine è diminuito l’assenteismo ed è aumentato l’indice di soddisfazione dei dipendenti”.
I risultati più importanti a lungo termine, secondo Cerina, sono però quelli intangibili e, primo fra tutti “l’avere sviluppato dei talenti che diverranno i leder nel futuro”. Non solo: “Abbiamo tolto la cultura di parlare per sensazioni, e oggi ci basiamo solo sui numeri, sui KPIs”. Tra gli aspetti positivi, Cerina sottolinea anche il numero elevato di persone che partecipano ai gruppi di miglioramento, e il fatto che, avendo una fabbrica più sicura ed efficiente, il posto di lavoro risulta più stabile e l’ambiente più sereno; inoltre, “abbiamo liberato risorse (tempo, soldi e idee) per supportare meglio il business”.
“La fase più critica l’abbiamo vissuta nel 2014-2015 – puntualizza il Direttore Operations –, quando abbiamo dovuto far diventare questa metodologia uno strumento di vita in fabbrica. L’obiettivo per il futuro è di farlo diventare un modo di pensare e non un obbligo”.
Un approccio pragmatico
Per introdurre la metodologia TPM, Lindt ha optato per un approccio molto pragmatico. Non è partita con un ‘mega’ progetto per risolvere subito tutti i problemi, ma ha approcciato il cambiamento in maniera semplice e per passi progressivi. “Prima di tutto abbiamo iniziato a misurare (se non misuri non migliori… e se non migliori, peggiori), così abbiamo istituzionalizzato una raccolta di indicatori, con un approccio bottom up da ciascuna linea di produzione – spiega Cerina –: vicino a ogni linea abbiamo messo un tabellone dove i capi linea potessero scrivere il risultato della giornata (in rosso se negativo, in verde se positivo), rendendo i lavoratori partecipi dell’andamento e i risultati visibili a tutti”.
Gli indicatori (PCS – Performance Control Systems) sono alla base di una riunione quotidiana tra capi linea, caporeparto e manutentori di area che discutono di come è andata la produzione nel giorno precedente; successivamente i capi di tutte le linee insieme si confrontano in una riunione giornaliera e, una volta alla settimana, vengono aggregati i risultati di tutte le linee e mandati alla direzione della produzione. Per le riunioni sono state definite delle regole semplici in modo da arrivare a un risultato utile in tempi brevi.
Per stimolare la rapidità è stato deciso che la sala riunioni non fosse particolarmente confortevole (piccola, senza finestre, senza un tavolo), che il responsabile di ogni reparto, una volta entrato in sala avesse pochi minuti per parlare (5 minuti di sicurezza, 10 delle efficienze e 5 di altro) e finito il proprio tempo lasciasse il posto al successivo. “All’inizio è stato difficile, ma poi si è capito che avendo poco tempo si doveva parlare solamente delle cose davvero importanti”.
La fase immediatamente successiva e propedeutica a tutto il resto del progetto è stata l’applicazione delle 5 ‘S’, una metodologia giapponese che tende a separare tutto ciò che non serve, ordinarlo, standardizzarlo e mantenerlo, “metodo validissimo per tutte le tipologie di azienda”, sottolinea Cerina. “Abbiamo iniziato con una grande pulizia generale, utile di per sé ma anche volutamente simbolica. In ogni reparto – scende nel dettaglio Cerina – abbiamo messo un’area recintata dove tutti hanno buttato le cose che non si usavano, magari conservate da anni e mai utilizzate; abbiamo buttato via carta, tubi, armadi, scatoloni…, la fabbrica è diventata molto più spaziosa e ordinata, cosa determinante per un’azienda alimentare sia per l’igiene sia per la sicurezza. Da qui la necessità di metter tutte le cose in ordine, per cui abbiamo deciso di eliminare tutti gli armadi chiusi e utilizzare solo scaffali aperti che permettessero di vedere immediatamente se le cose fossero in ordine, con tutti gli attrezzi appesi al posto giusto per facilitare il loro reperimento soprattutto al momento di cambiare il formato nelle linee. Le cassette dei nostri meccanici oggi sembrano quelle di una sala operatoria!”. E siccome “l’ordine fisico favorisce l’ordine mentale”, nello stabilimento si è proceduto alla separazione delle zone basandosi sul visual management, così ogni parte della fabbrica oggi ha delle aree delimitate da strisce per indicare i camminamenti, i parcheggi di diversi colori per i contenitori dei rifiuti, per i carrelli e così via, “strisce fatte con lo scotch per poterle spostare secondo necessità; all’inizio ci sono stati vari spostamenti, ma ora le delimitazioni sono stabili”.
Anche nei reparti degli uffici sono state implementate le 5 ‘S’, una pulizia sia fisica sia digitale (“abbiamo gettato tonnellate di carta e liberato molti gigabyte dai dischi fissi”). Nel caso dei file è stata anche definita una metodologia per la nomenclatura in modo da rendere immediatamente comprensibile il contenuto, quando è stato creato e chi l’ha creato, ottenendo un archivio strutturato ed univoco. Periodicamente ven- gono fatti degli audit per verificare quanto le 5 ‘S’ siano rispettate.
“Inizialmente – prosegue il suo racconto Cerina – siamo partiti con due aree dove volevamo trovare dei successi facili da mostrare a tutti, creando dei casi positivi. Ma non tutto è andato come avremmo voluto, abbiamo anche sbagliato: delle due aree individuate una è stata di grande successo e una di insuccesso (non avevamo applicato bene la metodologia, siamo stati troppo flessibili e abbiamo avuto qualche resistenza da parte di alcuni operatori)”.
Seguendo la metodologia TPM, si è iniziato ad ottenere un primo miglioramento dell’efficienza delle due linee. Questo successo ha creato un clima favorevole, “anche perché abbiamo enfatizzato e celebrato il risultato con una grande cena invitando tutti gli addetti alla linea (solo quella che ha raggiunto il risultato) e abbiamo scoperto che molte persone erano fiere del lavoro che svolgevano, e contente di poterlo manifestare. E dopo questo pilota molti hanno chiesto di fare il percorso di miglioramento”. Nel 2011 Lindt ha avviato l’applicazione ortodossa della metodologia estendendola a tutta la fabbrica lavorando per macro aree dette pilastri.
Gli 8 pilastri
Una volta implementati i KPIs e le 5 ‘S’ (“le fondamenta”), “a sostenere il tetto della nostra ‘nuova fabbrica’ sono 8 pilastri (introdotti tra il 2013 e il 2014). I pilastri sono rappresentati da specialisti, una sorta di consulenti interni che hanno imparato bene la metodologia e la insegnano a tutti gli altri, illustrando anche come utilizzare diversi metodi di risoluzione dei problemi come l’analisi di Pareto, i cinque perché, le schede kaizen, …”.
Gli 8 pilastri sono i seguenti.
Autonomous Maintenance: insegna alle persone della linea a tener cura della macchina (pulisci, ispeziona, lubrifica), per fare in modo che le macchine non si fermino per guasti evitabili. Per fare questo si parte con una pulizia inziale di tutte le macchine, osservando con attenzione dove si è sporcata; nel caso si sporchi sempre nel medesimo punto significa che si è di fronte a un difetto, conseguentemente si farà particolare attenzione a quella parte della linea durante i successivi interventi di pulizia oppure si cercherà una soluzione per ovviare al problema ricorrente.
Planned Maintenance: consiste nell’istituzio nalizzare la manutenzione preventiva, studiata specificamente macchina per macchina a seconda dell’intensità di utilizzo o imparando dalla storia dei guasti di ciascuna macchina; una programmazione che prende costantemente dati dalla realtà. Focus Improvement: è il cosiddetto ‘pilastro cacciatore’, che si occupa di verificare gli spechi, le perdite di prodotto, tempo, manodopera.
Training & Education: basandosi sulle problematiche sorte a causa della non conoscenza di alcune persone, organizza dei piani di formazione. I lavoratori delle linee sono stati chiamati a fare dei corsi base di meccanica, di elettricità, di trasmissioni e di pneumatica. “Per ogni posizione abbiamo creato un profilo ideale e ogni lavoratore è stato mappato per capire le lacune di ciascuno – chiarisce Cerina –. Ogni dipendente ha fatto un’autovalutazione e un’altra valutazione è stata affidata al caporeparto. Le due schede sono poi state messe a confronto in presenza di ‘un arbitro’, ovvero una persona dell’HR. In questo modo abbiamo mappato tutte le posizioni di fabbrica: produzione, manutenzione e logistica e fissato dei piani formativi specifici per persona”.
Quality Maintenance: cioè mantenimento della qualità. In questo caso si parte dai reclami dei consumatori e dai reclami delle non conformità interne (quando un prodotto passa da un reparto all’altro e qualche cosa non corrisponde alle necessità). Da qui si dà il via a dei processi di miglioramento mettendo assieme le competenze di diverse funzioni (produzione, qualità, ingegneria).
Early Management: quando si installa una nuova linea, imparando dagli errori fatti in precedenza, si cerca di partire con i minori problemi possibili, cercando di arrivare all’ottimizzazione della linea in tempi brevi. Safety: visti i grandi progressi fatti fino a oggi, ora in Lindt non ci si focalizza più solo sugli infortuni, ma sugli accident (“perché ogni accident potrebbe trasformarsi in un infortunio; operiamo sulla prevenzione”). TPM office: estende le 5S anche negli uffici e mira a migliorare l’efficienza delle attività amministrative.
Per la sicurezza un metodo particolare
Sull’aspetto sicurezza forse non è stata solo la metodologia Lean ad aiutare Lindt, ma un grande cambiamento culturale messo in atto con un sistema di raccolta di suggerimenti da parte dei lavoratori, che si basa su un approccio bottom up. “Abbiamo acquisito un software che ci permette di raccogliere i suggerimenti dei dipendenti relativamente a elementi o fatti potenzialmente pericolosi in fabbrica o negli uffici – spiega Cerina –. Per le segnalazioni i dipendenti possono usare sia il PC di reparto sia un totem posizionato presso la mensa sia il proprio PC di casa poiché si tratta di un sistema web aperto a tutti i coloro che dispongono di una specifica password. All’interno del sistema si possono segnalare per esempio il pericolo di scivolare a causa di un rubinetto che perde in una determinata linea, così come la caduta di un pallet che ha messo a rischio qualcuno, si possono semplicemente evidenziare mancati infortuni o miglioramenti possibili. Queste segnalazioni entrano in un sistema, by-passano tutti i capi intermedi e arrivano tutti i giorni al responsabile sicurezza e a me; ogni giorno, per ogni segnalazione (circa 1.500 all’anno) il responsabile della sicurezza manda, a chi l’ha fatta, un riscontro in cui spiega il piano d’azione predisposto, chi ne è responsabile e la data entro la quale sarà attuato (il lavoratore in questo modo vede che la sua segnalazione è stata presa in considerazione)”.
A questo è stato abbinato un sistema di incentivazione che dopo ‘n’ segnalazioni prevede un instant win, nello specifico 20 euro spendibili al negozio aziendale, inoltre coloro che segnalano di più, e in modo appropriato, hanno anche un altro premio, “ambitissimo qui da noi”, che è la possibilità di parcheggiare all’interno dello stabilimento. “Tutto ciò – racconta il manager – ha creato un volano di partecipazione positiva e di attenzione che ha contribuito notevolmente a migliorare la consapevolezza diffusa e la cultura della sicurezza. All’inizio questo metodo ha trovato qualche resistenza da parte dei capi intermedi che si sentivano pressati sia dall’alto che dal basso, così come è stato necessario un confronto con i sindacati che ritenevano che le segnalazioni andassero inviate prima a loro, ma dato che settimanalmente fornivamo loro un resoconto completo delle segnalazioni stesse hanno concordato che il sistema non aveva lo scopo di nascondere gli eventuali problemi, ma anzi quello di risolverli in modo serio e trasparente”.
Sempre per promuovere la sensibilità alle problematiche della sicurezza, Lindt ha instaurato la ‘settimana della sicurezza’, durante la quale vengono organizzati diversi eventi sull’argomento. Tra questi ‘la caccia al rischio’, “una sorta di caccia al tesoro: disseminiamo numerose ‘non conformità’ su una linea non in uso e chiamiamo i lavoratori a osservare e segnalare tutto ciò che non va bene, allenandoli a vedere tutto ciò che non è a norma; chi ottiene i migliori risultati percepisce un piccolo regalo utile (l’estintore da auto, lo strumento per gonfiare i pneumatici, …). All’ultima caccia organizzata hanno partecipato più di 200 dipendenti”. “Grazie a questo lavoro di sensibilizzazione siamo passati da 49 infortuni del 2010 a 2 nel 2014 e 1 nel 2015”, ribadisce con soddisfazione Cerina.
Una nuova sfida
Lindt per implementare il metodo Total Productive Maintenance si è avvalso di alcuni consulenti esterni, “ma ci siamo posti l’obiettivo di far valutare il sistema implementato da un ente giapponese che fa parte del ministero dell’Industria (JIPM – Japanese Insitute of Planned Maintenence) e che sono venuti a giugno e a dicembre dello scorso anno per valutare il nostro operato e il risultato è stato positivo”. Lindt, infatti, ha superato il primo assessment ottenendo 78 punti (per superare ‘l’esame’ della commissione giapponese ne bastano 70) ed è la prima fabbrica del gruppo a ottenere questo risultato. “Sono cinque i livelli da raggiungere, attualmente abbiamo superato il primo, ma vogliamo scalarli tutti – afferma Cerina –. Certo ogni step avrà nuove difficoltà da superare. Tra due anni – conclude – verranno di nuovo i consulenti giapponesi e vorranno vedere molta più naturalezza nell’applicazione della metodologia.Una nuova sfida; ma l’avere un obiettivo, raggiungerlo e porsi nuovi obiettivi, genera la motivazione necessaria”.
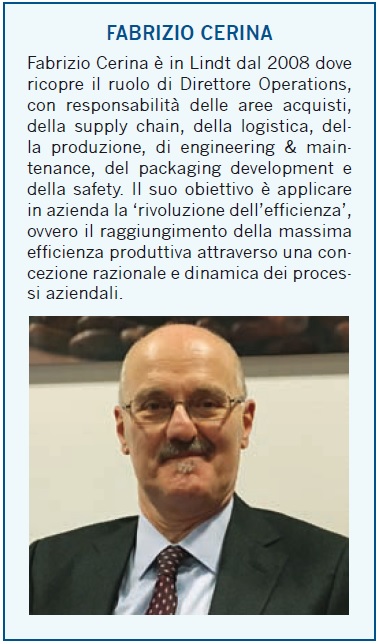
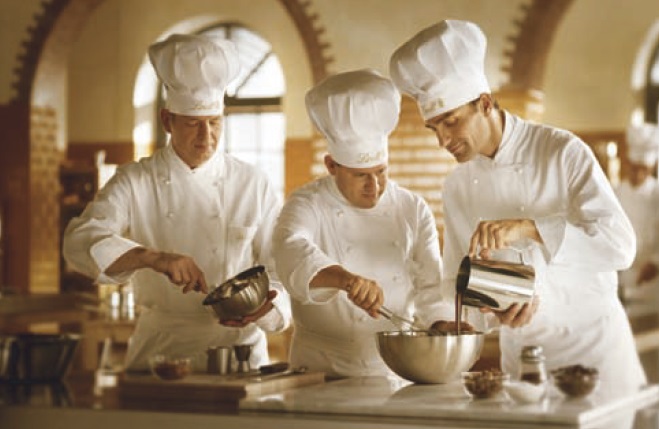
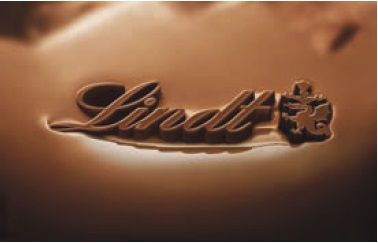
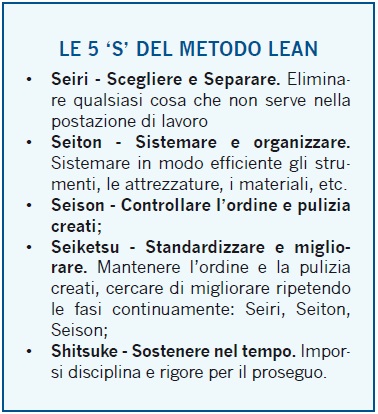
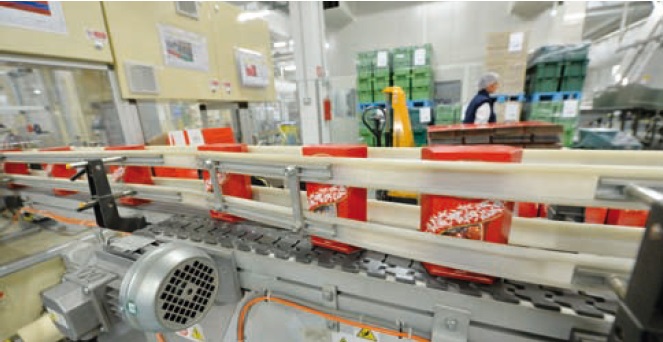