Prevenire i guasti con la manutenzione predittiva
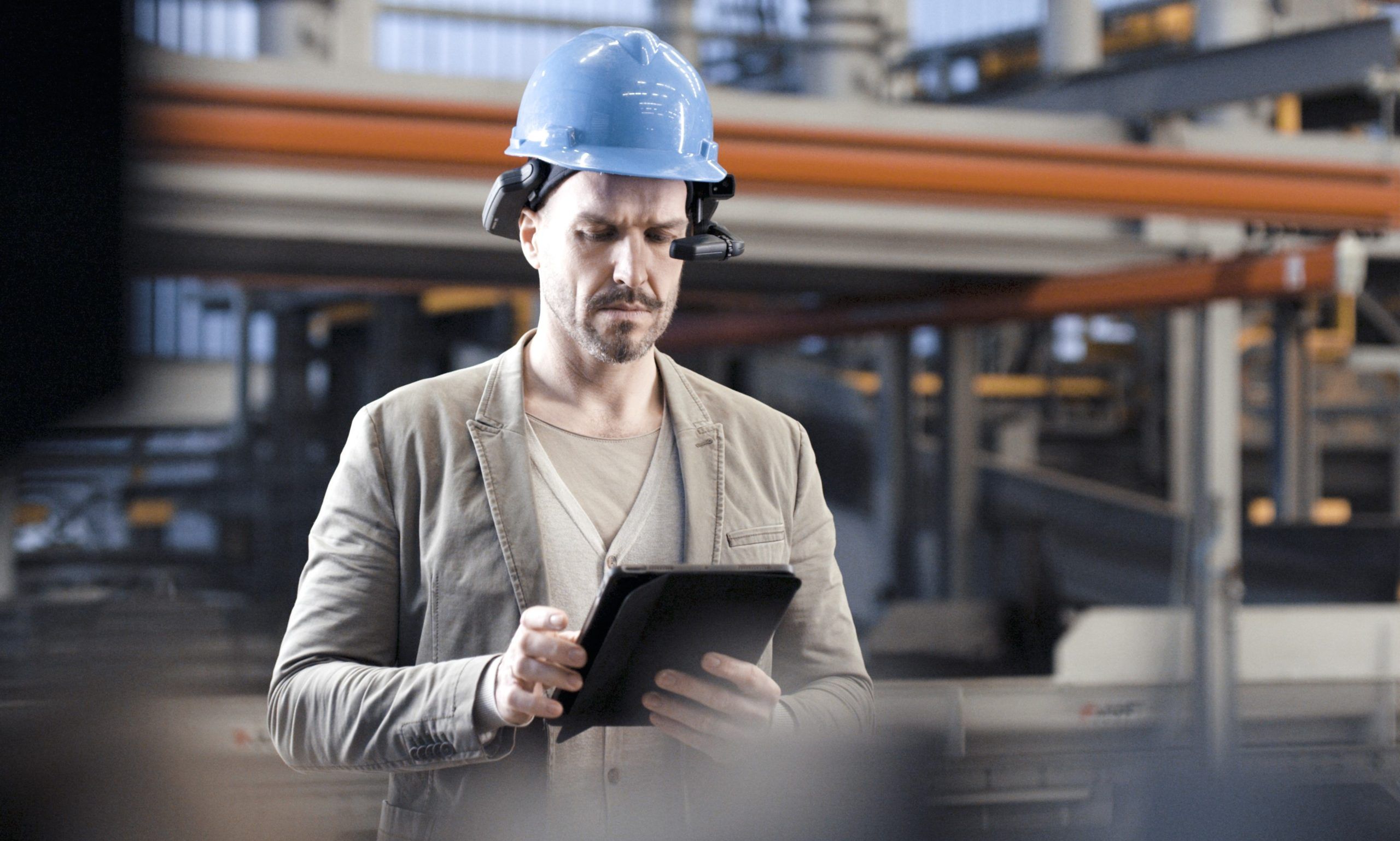
Comunemente, con il termine “guasto” si indica la cessazione dell’attitudine di un dispositivo ad adempiere alla funzione richiesta, ovvero una variazione nel livello di prestazione tale da renderlo inservibile per l’utilizzo al quale era destinato. Una prima, e più generale, classificazione dei guasti li vede suddivisi in: parziali (determinano un degrado nelle prestazioni del dispositivo tale, però, da non comprometterne del tutto la funzionalità); totali (causano una variazione delle prestazioni tale da impedire il regolare funzionamento).
Una divisione molto utilizzata per caratterizzare i guasti di un impianto industriale avviene in base alla natura del dispositivo oggetto del guasto stesso: meccanico, elettrico o informatico. Esistono, poi, numerose altre, e più dettagliate, classificazioni in base alla loro importanza, piuttosto che all’impatto sul contesto industriale o alle conseguenze per gli operatori.
Una specifica branca della teoria dell’affidabilità si occupa di questi studi, a cui si rimanda per eventuali approfondimenti che qui non trattiamo. Tuttavia, per ogni tipologia di guasto (comunque classificata) il tasso di accadimento (in letteratura failure rate) presenta un andamento nel tempo pressoché uguale (Figura 1): una prima fase in cui è alto, ma tende rapidamente a decrescere fino a raggiungere un livello stazionario (di solito questo momento ha una durata breve rispetto alla vita del dispositivo e i guasti sono detti anche “mortalità infantile”); una seconda fase, in cui è pressoché costante (questa fase ha una durata comparabile alla vita del dispositivo e viene detta “vita utile”); infine, una terza fase in cui cresce rapidamente (anche questa ha una durata breve rispetto alla vita del dispositivo e i guasti sono detti anche di “fine vita”).
I guasti che occorrono nella prima fase sono dovuti sostanzialmente a difetti di costruzione dei macchinari che costituiscono l’impianto (o sue sotto parti) e che si manifestano durante i primissimi periodi di impiego; talvolta, per intercettarli si sottopongono i dispositivi a screening termici o vibrazionali. Le criticità che occorrono, invece, nella terza fase sono dovute al degrado delle prestazioni dei macchinari, causato dall’approssimarsi del fine vita. In entrambi i casi, dato l’elevato numero di guasti e la loro natura, non conviene mettere in atto politiche di manutenzione che, invece, contraddistinguono la seconda fase. Di fatti, la manutenzione, definita come la “combinazione di tutte le azioni tecniche, amministrative e gestionali, eseguite durante il ciclo di vita di un elemento destinate a preservarlo o a riportarlo in uno stato in cui possa eseguire la funzione richiesta” (norma UNI EN 13306), è sviluppata nel periodo di vita utile del dispositivo.
La manutenzione come funzione di business
Quest’attività è una funzione fondamentale dell’intero processo produttivo, che garantisce la continuità e la qualità della produzione rendendo disponibili gli impianti e le apparecchiature nel rispetto delle politiche aziendali in termini di sicurezza, ambiente e qualità. La sua missione non si esaurisce con la mera esecuzione delle attività manutentive e richiede organizzazione, conoscenza e applicazione di tecnologie di eccellenza. Si parla, quindi, di Ingegneria della manutenzione, intesa come una vera e propria funzione di business all’interno dell’azienda, con l’obiettivo non solo di garantire la continuità operativa degli impianti, ma anche di allungarne la vita utile e di ridurne i costi di manutenzione perseguendo politiche di miglioramento continuo. In tale ottica, risulta fondamentale la conoscenza degli impianti e dei macchinari, onde gestire le priorità degli interventi in base alle criticità ed essere in grado di risalire dall’effetto alla causa per ogni tipologia di guasto. La metodologia Failure models effect and criticality analysis (Fmeca) consente di determinare l’affidabilità di un impianto o di una sua sotto-parte durante tutto il ciclo di vita e di individuare gli elementi più critici. È altresì importante registrare e tener traccia degli interventi eseguiti, per poter correggere e migliorare le attività future. Le politiche di manutenzione tradizionalmente si suddividono in due categorie: correttiva e preventiva. La prima, detta anche “a guasto”, si basa sul principio di intervenire in modo tempestivo per ridare all’impianto la piena funzionalità. È intuitivo capire che tale politica di manutenzione è applicabile con successo solo a impianti e macchinari relativamente semplici e non critici, per i quali ci si può permettere un tempo di fermo non stimabile a priori e la riparazione dei guasti è quasi sempre fattibile in tempi ritenuti accettabili dalle politiche aziendali. Essa ha costi contenuti (si spende solo a fronte di un guasto e per ripararlo) e non prevede strutture organizzative e di pianificazione; di contro, genera inefficienza nella gestione delle squadre di manutenzione (che intervengono solo a fronte di un guasto) e non consente un corretto allestimento del parco ricambi. La seconda, detta anche “ordinaria”, mira, invece, a prevenire i guasti mediante azioni prefissate e svolte indipendentemente dalla loro occorrenza, quali per esempio: pulizie di filtri, sostituzioni di accessori consumabili o di parti usurabili, sostituzione di sotto-parti a vita limitata. Essa si suddivide a sua volta in due categorie: manutenzione predeterminata, che esegue azioni decise a priori a intervalli prefissati (di tempo o di utilizzo), indipendentemente dallo stato degli impianti e degli eventuali accessori e sotto-parti da sostituire; manutenzione condizionata (in letteratura è indicata come Condition based maintenance), che ugualmente esegue azioni decise a priori, ma al verificarsi di specifiche condizioni (anche esse determinate a priori) degli impianti o macchinari. Entrambe le metodologie necessitano di una struttura organizzativa e di pianificazione e aggiungono costi fissi al programma di manutenzione. Tuttavia, riducono sensibilmente i guasti migliorando la disponibilità degli impianti e consentono una gestione più efficiente sia delle risorse umane sia del parco ricambi. Un corretto programma prevede la giusta combinazione delle metodologie esposte, nell’ottica di massimizzare la disponibilità degli impianti e ridurne i costi di gestione. Il successo di ogni politica di manutenzione può essere misurato in termini di quanto previene i guasti, determinando così un incremento della disponibilità degli impianti, nell’ottica di un corretto bilanciamento tra costi e performance. A tal fine esistono numerosi Key performance indicator (Kpi) correntemente utilizzati, e quello che garantisce la maggiore aderenza ai processi produttivi è l’Overall equipment effectiveness (Oee).L’articolo integrale è pubblicato sul numero di Ottobre 2022 di Sistemi&Impresa.
Per informazioni sull’acquisto di copie e abbonamenti scrivi a daniela.bobbiese@este.it (tel. 02.91434400)
Antimo Angelino è Membro della Commissione Uninfo CT 519 ‘Tecnologie abilitanti Industria 4.0’, Leader Gruppo di Lavoro 4 ‘Digital Twin’, Membro ISO/IEC JTC1 SC41 ‘Internet of Things & Digital Twin’, Head of Delegation Italy
kpi, manutenzione predittiva, tecnologia