Manutenzione predittiva e IoT per evitare i fermi degli impianti
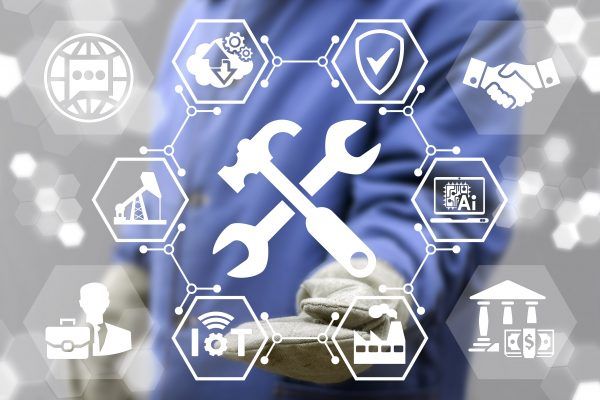
La manutenzione industriale è da sempre uno dei fattori più importanti in un’azienda, al fine di mantenere elevato il livello di sicurezza di un macchinario o di un impianto, garantire efficienza e produttività ed evitare che si verifichino guasti e malfunzionamenti che potrebbero portare a blocchi della produzione duraturi e prolungati, dovuti a sostituzioni e riparazioni. Oggi, possiamo parlare di una vera e propria evoluzione: la manutenzione predittiva.
Infatti, fino a qualche decennio fa, si interveniva su un impianto nel momento esatto in cui esso si rompeva, provocando tempi di attesa imprevisti, aumento dei costi e perdita di produzione. Adesso, la fabbrica del futuro si proietta in uno scenario completamente innovativo e tecnologico, nel quale, connettendo gli impianti attraverso IoT, raccogliendo e analizzando dati tramite algoritmi di Intelligenza Artificiale, è possibile prevedere anomalie che si presenteranno su un componente o un macchinario.
Avresti mai pensato, in passato, che un semplice dispositivo come uno smartphone o un tablet avrebbe potuto avvisarti quando qualcosa nella tua fabbrica sta per accadere? E suggerirti come fare per evitarlo o quali azioni correttive sarebbe più opportuno applicare, quando tutto sembra apparentemente funzionare? Ecco, la manutenzione predittiva, in sostanza, è questo: una manutenzione intelligente in grado di prevedere cosa accadrà nel futuro, considerando lo stato attuale del macchinario.
Grazie alla sinergia tra la raccolta dei dati e l’analisi dei segnali e degli allarmi, il cliente oggi ha a disposizione dashboard con le quali può consultare, mediante tablet o smartphone, lo stato di salute dei suoi impianti.
Gli obiettivi preposti sono stati raggiunti con successo. Infatti, il cliente sta riscontrando un abbattimento dei costi relativi alla manutenzione di circa il 25-30%, eliminando attività manutentive non necessarie e indirizzando più efficacemente le risorse.
Inoltre un aumento della produttività ed efficienza del 25% grazie a un’attenta analisi dei downtime e delle performance delle macchine.
Tutto questo si è tradotto in un forte impatto sull’estensione e la massimizzazione della vita dei beni e degli impianti e in un notevole vantaggio competitivo.
La gestione strategica del dato
In questo contesto, si può affermare che il dato sia il nuovo asset strategico per un processo manifatturiero ottimizzato e digitalizzato. Ma un efficace sistema di manutenzione predittiva non dipende solo da fonti selezionate e aggregate di dati; elemento fondamentale e necessario riguarda l’analisi del dato per estrarre da esso informazioni utili. I dati possono essere di diverso tipo e provenire da più fonti, interne ed esterne, come per esempio serie statistiche sullo storico del funzionamento dei macchinari, informazioni contestuali come fattori esterni che potrebbero influenzarne le prestazioni, input ottenuti in real time dalle interazioni con altri oggetti e con il mondo fisico.Soluzioni che rappresentano un vantaggio competitivo
L’implementazione di queste soluzioni end to end, viene realizzata dai system integrator piuttosto che dai vendor delle piattaforme IoT, Cloud, ecc. La particolarità di queste figure è che possiedono le competenze trasversali adatte per strutturare interi progetti specifici in azienda e sfruttare la scalabilità dei progetti. Così il cliente può partire con piccole sperimentazioni su una macchina o parti di impianto, per poi estenderle in un secondo momento. Inoltre, sfruttando le loro competenze in ambito ICT, come Edge computing, Big data e Analytics, assumono un ruolo fondamentale anche ex post, in quanto gli innumerevoli dati prodotti dalle piattaforme 4.0 devono successivamente essere gestiti e interpretati in modo tale che il cliente finale possa trasformarle in un vantaggio competitivo. ECSA, partner tecnologico e system integrator, ha strutturato una serie di soluzioni per monitorare e prevenire i fermi degli impianti che spesso provocano interruzioni nella produzione e tempi di ripartenza molto lunghi.Dall’analisi delle performance all’abbattimento dei costi
Un esempio di progetto di successo è stato realizzato per un importante cliente operante nel settore siderurgico. La soluzione implementata all’insegna della manutenzione predittiva ha visto l’utilizzo dell’IoT e di altre tecnologie abilitanti dell’Industria 4.0. Dopo un’attenta analisi delle esigenze e delle caratteristiche degli impianti, il progetto è stato suddiviso in due fasi. Nella prima fase sono stati installati sensori per rilevare parametri di processo, quali temperature, vibrazioni e pressioni. I dati raccolti vengono trasferiti a un Edge Gateway in grado di filtrarli, analizzarli, e inviare alert tramite SMS o email agli operatori di manutenzione. Inoltre mediante un sistema SCADA (un sistema informatico distribuito per il monitoraggio e la supervisione di sistemi fisici) è possibile memorizzare i dati, visualizzarne i trend ed eseguire delle analisi di performance, quali Overall Equipment Effectiveness (OEE, la misura di efficacia di un impianto) e downtime. Successivamente, in una seconda fase, il sistema sarà ampliato trasferendo i dati filtrati e normalizzati, a una piattaforma di Big data management con l’obiettivo effettuare analisi predittive mediante algoritmi di Machine learning.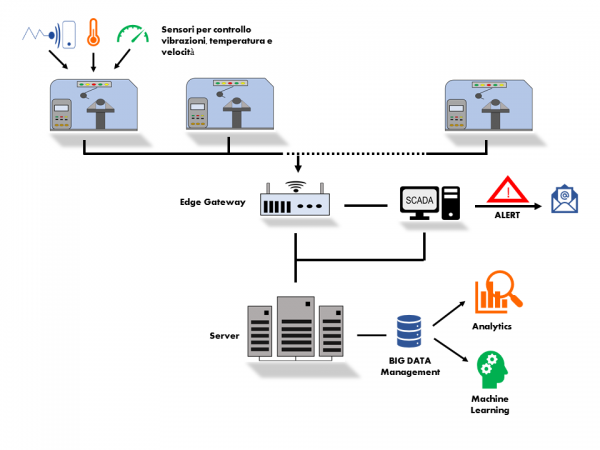
Marketing Specialist di ECSA
analytics, big data, Intelligenza Artificiale, IoT, manutenzione predittiva