Dall’idea al prodotto: software integrati per team interconnessi
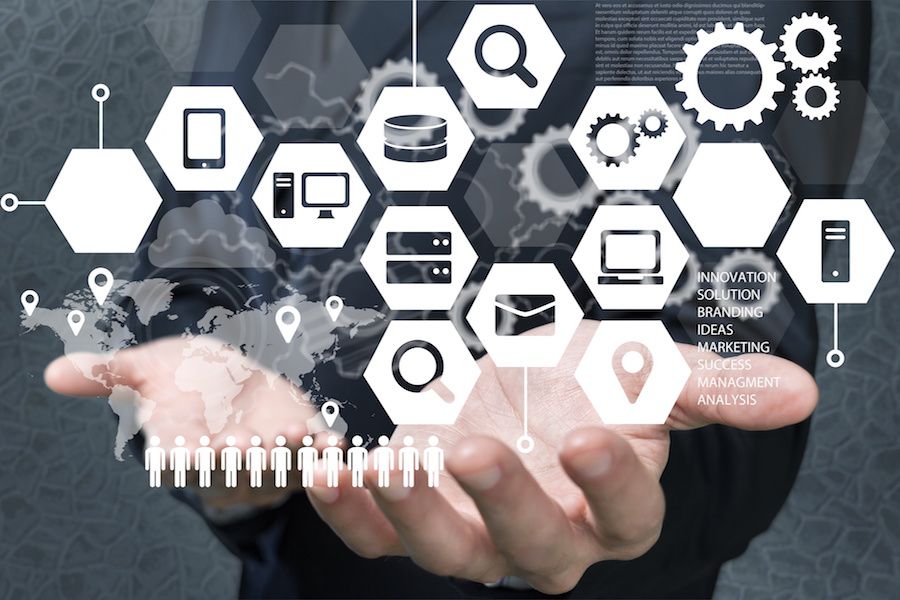
Nella Smart factory del futuro, progettazione e produzione non sono più fasi distinte e separate. La rivoluzione digitale ha imposto la condivisione delle informazioni e l’automatizzazione dei processi in tutte le fasi di sviluppo, dall’idea al prodotto.
Per stare al passo con la trasformazione dell’Industria 4.0, gli sviluppatori possono utilizzare strumenti che vanno oltre le tradizionali soluzioni di disegno o di modellazione 3D. Cambiano i prodotti e cambiano le geometrie progettuali: la nuova parola d’ordine è “interconnettività”.
I moderni sistemi per la progettazione assistita dal computer – CAD (Computer Aided Design) – non si limitano più a generare disegni per la produzione. Nelle fabbriche intelligenti gli sviluppatori hanno bisogno di sistemi integrati, che producano dati multidisciplinari e utilizzabili nello stesso momento da più funzioni: visualizzazione, convalida, analisi dei costi, pianificazione, gestione dei dati, produzione. E ancora: controllo di qualità, documentazione, sviluppo del packaging e marketing.
Con sistemi integrati come CAD 3D SolidWorks, il software per la progettazione proposto da SolidWorld, ogni fase dell’attività può essere svolta attingendo agli stessi dati e in modo pressoché contestuale. “Rendendo i dati CAD 3D il Dna di base dell’intera azienda, le aziende di produzione possono investire in maggiore efficienza, collaborazione e innovazione, per ottenere un sistema integrato di sviluppo dei prodotti”, spiegano gli esperti di SolidWorld.
Utilizzare un sistema integrato significa poter accedere e lavorare con gli stessi dati CAD contemporaneamente all’interno di un unico ambiente nativo, risparmiando tempo e riducendo i costi della progettazione per tutto l’arco del processo.
Ridurre i costi e aumentare la produttività
L’impiego di un software integrato promette di accorciare i cicli di sviluppo e produzione e ridurre i tempi di immissione sul mercato. Anziché lavorare in modo sequenziale, l’azienda può adottare un approccio simultaneo, che consente non solo di accedere a tutte le funzioni ma anche di lavorare con i dati più recenti perché aggiornati in modo automatico a ogni modifica del progetto. Ogni funzione può lavorare senza necessità di importare, esportare, tradurre o convertire i dati. Anziché partire da un insieme di disegni tecnici, il personale di produzione è in condizioni di accedere subito al modello 3D principale, risolvere eventuali problemi fin dalle prime fasi del processo e integrare le modifiche apportate da qualsiasi reparto. Abbreviare i cicli di progettazione, poi, significa anche eliminare attività e costi non necessari. Senza contare i risparmi dovuti al minor numero di prototipi fisici e guasti sul campo: con un unico sistema in uso a più utenti, anche i costi di manutenzione e di formazione interna si riducono. Ulteriore vantaggio di un sistema integrato di sviluppo dei prodotti 3D come SolidWorks, ora promosso con un prezzo speciale, è il fatto che riduce al minimo la probabilità di errori umani nel corso del processo. Sia perché, dopo ogni modifica, il modello viene subito aggiornato, sia perché gli strumenti di simulazione consentono ai progettisti di effettuare un controllo accurato delle prestazioni, eliminando il rischio di errori in fase di revisione. La nuova soluzione SolidWorks 2020 offre, infatti, una gamma di strumenti di analisi e di simulazione pensati per prevedere il comportamento dei prodotti nel mondo reale, collaudando i modelli CAD in ambiente virtuale. Con importanti novità in ambito CAD 3D. Lo strumento Visualize consente di sfruttare al meglio i dati per creare contenuti di qualità fotografica, mentre le soluzioni Electrical semplificano la progettazione di prodotti elettrici grazie a strumenti specifici per ingegneri e interfacce intuitive. Infine, PDM, Product Data Management, permette ai team di archiviare e indicizzare i dati di progettazione in sicurezza per collaborare ai progetti anche da luoghi diversi. C’è un effetto positivo sul lavoro di gruppo: lo sviluppo simultaneo del prodotto, infatti, costringe alla collaborazione. E un ambiente collaborativo è un’ottima fucina di idee, concentrata più sulle opportunità che sui problemi da risolvere. Un software integrato, in definitiva, garantisce anche un team più integrato: agile nello sviluppo dei prodotti, flessibile nei progetti e libero di collaborare per ispirare i prodotti innovativi del futuro.CAD 3D SolidWorks, Fabbrica 4.0, in evidenza, sistema integrato, smart factory