Manifatturiero: 6 falsi miti che frenano le aziende sull’innovazione
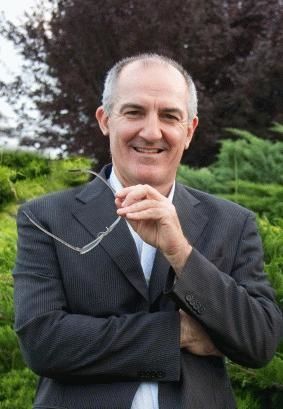
La Fabbrica 4.0 sta diventando una realtà, ma le imprese italiane spesso non sanno di poter migliorare la propria produzione con le nuove tecnologie
“La Fabbrica 4.0 sta diventando una realtà, anche se molte aziende italiane non sanno che possono innovare i processi produttivi e, soprattutto, non sanno come farlo. Questo si traduce in un ritardo per il settore manifatturiero italiano che sarà difficile colmare in futuro: la forbice tra le aziende che hanno innovato e quelle che sono rimaste ancorate a metodi tradizionali si è aperta molto negli ultimi anni ed è destinata a crescere ancora”. Ne è convinta Tecnest, azienda specializzata nella fornitura di soluzioni informatiche e organizzative per la pianificazione, il controllo e la gestione dei processi di produzione e della supply chain.
“Spesso le aziende non innovano perché non sanno che ci sono metodi di gestione che potrebbero interessare proprio loro, perché non conoscono o sottovalutano i reali vantaggi, pensano di perdere la propria flessibilità operativa o, semplicemente, perché non credono che ci sia qualcuno che possa migliorare la qualità del proprio lavoro – dice Fabio Pettarin, uno dei soci fondatori e Presidente di Tecnest –. In realtà quello che noi proponiamo non è introdurre un software per ‘burocratizzare’ le metodologie lavorative, ma rendere più razionale e agile la gestione dei processi produttivi. Oggi esistono strumenti che possono migliorare di molto la produttività delle fabbriche anche con semplici accorgimenti. Il nostro lavoro consiste non solo nel fornire un software ‘preconfezionato’, ma anche consulenza e progetto. Accompagniamo per mano il cliente nella trasformazione, proponiamo soluzioni specializzate che si possono affiancare e integrare a quelle già esistenti e a cui magari l’azienda non è risposta a rinunciare. Il tutto senza stop alla produzione’.
I falsi miti
Ecco quindi i principali falsi miti sull’innovazione nel manifatturiero. Il primo falso mito è che software e innovazioni riguardano solo le aziende che si occupano di IT, automazione industriale o tecnologia. “Qualsiasi azienda manifatturiera può innovare, qualsiasi sia il settore in cui lavora: tra i nostri clienti abbiamo realtà del settore automotive, metalmeccanico, elettronico, ma anche aziende tessili, del fashion, chimico-farmaceutiche o che producono cosmetici, salviettine umidificate, candele di cera… Più che cosa si fa, a noi importa il come”, spiega Pettarin.
Un’altra convinzione errata è che l’innovazione riguarda solo imprese di grandi dimensioni e con clientela internazionale: “Molti tra i nostri clienti sono aziende medio-piccole che si occupano di un settore di nicchia. Anzi, spesso sono queste le realtà che beneficiano prima e meglio del nostro intervento, in quanto avendo minori risorse riescono a organizzarle in modo ottimale, riuscendo così a migliorare le performance e il proprio servizio al cliente finale”.
Un altro falso mito molto diffuso è che l’introduzione dell’informatica in fabbrica comporti la riduzione dei posti di lavoro: “Nella nostra esperienza non è così. Se la fabbrica diventa più efficiente, non si licenziano persone: piuttosto si cambiano di ruolo e, spesso, si organizzano corsi di formazione interni per portarli a fare dei lavori più qualificanti”, dice il presidente di Tecnest.
Il quarto errore è pensare che i sistemi informativi aziendali siano troppo rigidi per adattarsi alle continue e, spesso, imprevedibili variazioni del mercato: “Al contrario i nostri software sono stati pensati proprio per dare la massima flessibilità nella pianificazione e gestione dei processi produttivi, attraverso funzionalità simulativo-interattive che permettono un confronto tra scenari alternativi. In questo modo eventuali imprevisti (dalla rottura di un macchinario a problematiche di fornitura) o ordini inattesi possano essere gestiti in poco tempo e con la massima flessibilità. Al mutare delle condizioni, ricreare il piano di produzione e riorganizzare il lavoro è più facile se a farlo è un sistema informatizzato”.
A volte le imprese non intraprendono un processo di innovazione tecnologica in fabbrica perché pensano che l’investimento in termini economici e di tempo sia troppo elevato: “Spesso le aziende non hanno tempo per fermarsi a ripensare alla gestione dei propri processi, anche perché quasi sempre si crede che per l’introduzione di un sistema come il nostro la produzione debba subire uno stop, con costi operativi molto elevati. Inoltre spesso un progetto di implementazione di un software di gestione della produzione viene confuso con la sostituzione in toto del sistema ERP o gestionale già esistente, con un relativo impatto economico notevole per l’organizzazione. In realtà il nostro intervento non richiede stop alla linea produttiva e spesso va a integrare, non a sostituire, il software ERP già esistente, focalizzandosi sul miglioramento dei processi di pianificazione e gestione della produzione. Trattandosi di un sistema cosiddetto dipartimentale, i tempi e i costi di implementazione, quindi, sono più contenuti. Il ritorno sull’investimento, infine, è rapido e dimostrabile in termini di maggiore efficienza in produzione, di performance sui processi e di competitività aziendale”, spiega il Presidente dell’azienda friulana.
Un’altra obiezione riguarda il fatto che questi sistemi sono molto complessi da usare e richiedono formazione specifica per i diversi ruoli aziendali: “In Tecnest abbiamo messo a punto un software role-based con un’interfaccia configurabile in base al ruolo delle persone che lo utilizzano. In questo modo ciascun utente, per esempio il responsabile della pianificazione della produzione, il responsabile di reparto, il responsabile acquisti ecc, non deve passare da una voce di menù all’altra, ma ritrova direttamente sul pannello di entrata all’applicazione tutte le informazioni di interesse e le applicazioni utili per il proprio ruolo aziendale e le proprie attività, migliorando la sua operatività quotidiana”.
I vantaggi di una svolta tecnologica in fabbrica non mancano: “Con una gestione unica di tutte le fasi è possibile prevedere in anticipo i processi, con risultati tangibili: l’affidabilità nelle date di consegna aumenta fino al 40%, l’efficienza di produzione cresce del 20%, mentre la percentuale di scarti e prodotti non conformi scende significativamente. I tempi decisionali a livello manageriale diminuiscono fino al 60%, dichiara Pettarin, che conclude: “Il software non sostituisce le persone, ma serve ad aiutarle: non esiste fabbrica senza un cervello umano”.
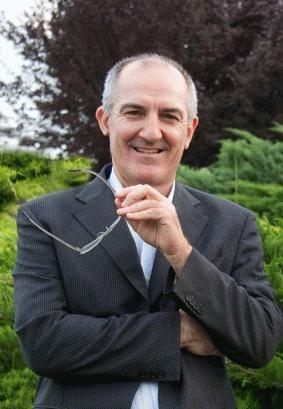