La comunicazione machine-to-machine come prevista da Industria 4.0
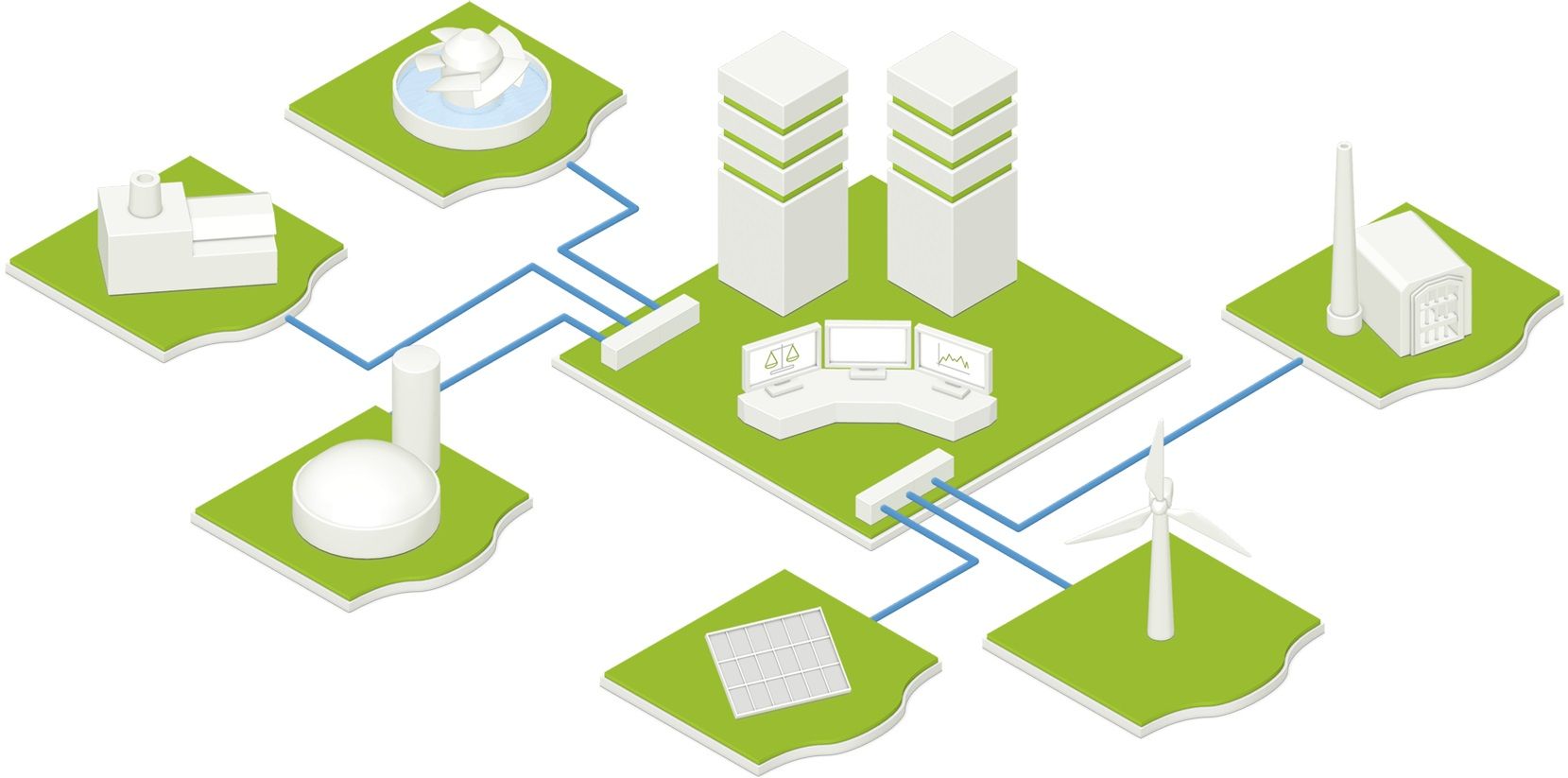
Nel dibattito sull’energia elettrica di domani, la ‘centrale elettrica virtuale’ è diventata una parola chiave. In futuro il modello di centrali elettriche di grosse dimensioni, meno versatili, verrà soppiantato da piccole unità di produzione decentralizzate come, per esempio, le centrali termoelettriche a blocco che producono elettricità e calore rispondendo il più possibile alle esigenze degli utenti.
Per non compromettere il rendimento complessivo di questo tipo di centrale elettrica virtuale, costituita da una serie di unità interconnesse, è importante un funzionamento corretto.
Gli impianti della 2G Energie, casa produttrice di centrali termoelettriche a blocco, sono a tal punto armonizzati fra loro che i tempi di inattività sono ridotti al minimo. Una rete intelligente e la comunicazione machine-to-machine contribuiscono a migliorare l’assistenza nella quotidianità lavorativa. Le soluzioni software smart diventano così sempre più importanti per le tecnologie che si occupano della fornitura decentrata di energia. Esse rappresentano nel futuro la premessa necessaria a un adeguato approvvigionamento energetico.
Per capire che la fornitura decentrata di energia rappresenta il mercato del futuro, basta guardare lo sviluppo della 2G Energy AG di Heek. L’impresa fu fondata nel 1995 e rappresenta oggi uno dei produttori leader in Europa di centrali termoelettriche a blocco. Come solution provider di sviluppo, produzione, gestione di progetti e assistenza, la 2G produce centrali termoelettriche a blocco con uno spettro di potenza che va dai 20 ai 4.000 kW. L’azienda conta 550 impiegati in tutto il mondo, distribuiti tra società madre e nuove controllate, è dal 2007 quotata in borsa e ha installato 4mila impianti in oltre 35 paesi.
Centrali termoelettriche a blocco come quelle sviluppate e prodotte dalla 2G – collegate fra di loro – costituiscono una centrale elettrica virtuale. Durante la loro progettazione e produzione, viene generata una grande quantità di dati di prodotto. Per far fronte alla crescente produzione dei propri impianti, la 2G Energy ha bisogno di dati principali di prodotto, distinte base e un catalogo dei pezzi di ricambio perfetti.
È per questa ragione che, qualche tempo fa, l’azienda ha introdotto la gestione dei dati di prodotto, ossia il sistema Product Lifecycle Management PRO.FILE (PDM/PLM) del produttore tedesco PROCAD. La 2G ha dunque scelto un sistema della nuova categoria “DMStec”: un sistema di gestione dei documenti che riproduce strutture tipiche complesse per l’ingegneria meccanica e l’impiantistica e che può essere usato sia come PDM che come DMS. Un gruppo di progetto ha introdotto progressivamente il sistema per singoli progetti di componenti in 3D. I dati CAD di un progetto sono stati trasferiti dal loro precedente luogo di archiviazione, la cartella del progetto sul server, in PRO.FILE.
Prima di introdurre il sistema PLM, la 2G archiviava i dati di prodotto sul server nelle cartelle di progetto. In questo modo venivano generati dati ridondanti, i modelli CAD non funzionavano più perché veniva modificato un percorso del file o qualcuno aveva spostato quest’ultimo. Risulta difficile rintracciare di volta in volta i dati aggiornati del modello e poiché la maggior parte dei pezzi di ricambio si trova nelle progettazioni, manca anche la base per ricavare dai modelli un catalogo dei pezzi di ricambio. Spesso, perciò, i progettisti gestivano i pezzi di ricambio in formato excel, cosa che comportava ulteriore lavoro.
Il sistema PLM consente ora ai progettisti di conservare in modo strutturato i modelli CAD con i dati di prodotto, ottenendo per le parti progettate delle distinte base corrette. D’altra parte, tuttavia, il sistema PLM va al di là di una semplice gestione dei dati CAD. Esso prevede anche il controllo del processo dei dati di prodotto e dei flussi d’informazioni. Se tale controllo viene esteso al di là dei confini aziendali, è possibile realizzare in tempo reale, sia a livello interno che esterno, un coordinamento in rete dei processi che accompagna l’intero ciclo di vita del prodotto.
Nella prima fase è stata attuata la comunicazione autonoma dei sistemi tecnici nel campo dell’assistenza. I moduli sono dotati di sensori che registrano nell’impianto il malfunzionamento o il guasto di un componente. Il software dell’impianto genera quindi un ticket di malfunzionamento redigendolo automaticamente nel sistema PLM. In questo modo s’attiva in automatico una procedura d’assistenza, diversamente da quanto accade fino a oggi dove i guasti venivano registrati telefonicamente. Il software archivia il ticket nel settore di competenza e il tecnico provvederà successivamente all’evasione: una comunicazione machine-to-machine grazie alla quale il produttore di centrali termoelettriche a blocco è riuscito a snellire il traffico della sua Hotline consentendogli di impiegare il personale tecnico in modo più mirato. Ciò si traduce per il cliente in un risultato: la sua centrale elettrica ritorna a essere di nuovo operativa in un batter d’occhio.
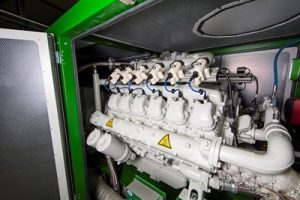
Trasparenza dei processi d’assistenza
Alla 2G Energy, il sistema PLM svolge la funzione di un data backbone che raccoglie tutti i dati principali di prodotto, le distinte base e il catalogo dei pezzi di ricambio. In questo modo esso crea le basi per una comunicazione machine-to-machine tra le centrali termoelettriche a blocco distribuite. Collegando il sistema con altre applicazioni aziendali, il produttore degli impianti realizza veri e propri scenari di Industria 4.0.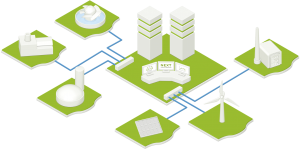