Sedili e cinture made in Sabelt. Gli artigiani della sicurezza

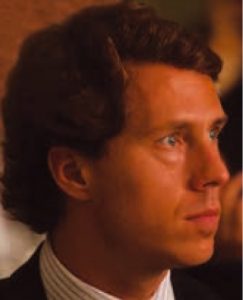
Artigiani attenti ai dettagli del prodotto
Massimiliano Marsiaj ci accoglie sulla soglia di una delle due sedi di Moncalieri, ma subito ci accompagna a visitare lo stabilimento produttivo a pochi minuti di strada di distanza, dedicandoci tempo prezioso proprio nel bel mezzo di una frenetica giornata di incontri che imporrebbero la sua presenza. In fabbrica il manager è a suo agio e ci guida nella visita delle linee produttive dove lavorano circa 150 addetti. “Sabelt ha mantenuto il suo Dna sportivo e lo ha trasmesso nelle auto di serie”, spiega il Vice Presidente dell’azienda mentre ci troviamo proprio in mezzo alla linea di produzione dei sedili in carbonio e vetroresina di Abarth. “Il sedile è composto da quattro parti: lo schienale, le schiume, le fodere e le giunture; il nostro lavoro consiste nell’assemblare i diversi componenti e di testarne l’utilizzo”, racconta con la passione tipica di chi passa ben poco tempo alla scrivania e buona parte a contatto con il prodotto per assicurare al cliente la miglior qualità.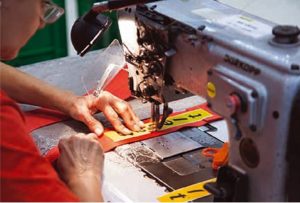
Digitalizzare conservando la tradizione
La linea produttiva più innovativa è però quella attualmente in preparazione: si tratta di una linea che permette a Sabelt di diventare protagonista della quarta rivoluzione industriale senza snaturare in nessun modo l’anima artigianale dell’azienda. Nonostante l’utilizzo massiccio di soluzioni digitali, infatti, il ruolo dell’uomo è ancora fondamentale: la tecnologia è solo uno strumento per poter svolgere al meglio, e con meno fatica, lo stesso lavoro di prima. A presentarcela sono tre giovani di Sabelt che da tempo lavorano al progetto e non vedono l’ora di spiegare ogni segreto della nuova linea, concedendo un attimo di pausa a Marsiaj che può così rispondere al cliente straniero che da tutta la mattina lo cerca con insistenza al telefono. Le linea è stata creata per i prodotti destinati alla Alpine Renault, la casa automobilistica francese specializzata nella costruzione di vetture sportive: per prima cosa l’operatore si deve autenticare con l’impronta digitale e la postazione si regola automaticamente secondo i suoi parametri biometrici; le operazioni da compiere non sono scritte su documenti cartacei, ma sono illustrate direttamente a video (“Uno dei nostri obiettivi è la gestione documentale digitale”, interviene Marsiaj) così che l’addetto sa che cosa prelevare; inoltre il software verifica che il componente prelevato sia quello corretto, perché l’operatore deve leggere l’etichetta con il Qr Code o il Barcode (in questo modo si tiene traccia di tutte le parti del prodotto finale).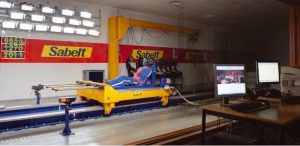
Cinture per la Formula 1 cucite a mano
Nonostante i sedili rappresentino la parte più importante del fatturato dell’azienda, Sabelt continua a fornire cinture di sicurezza per otto team di Formula 1, un’attività, quest’ultima, che stimola la continua ricerca di soluzioni innovative e i cui risultati si ripercuotono su tutti i prodotti dell’azienda. A creare le cinture sono alcune addette che, sedute a un tavolo, confezionano a mano ciò che contribuisce a garantire la sicurezza dei piloti che sfrecciano a oltre 300 km/h in pista. “Essere partner delle scuderie di Formula 1 ci assicura una grande visibilità”, ammette Marsiaj, mentre ci fa toccare con mano il prodotto finito e ci spiega che ogni pilota ha il suo set di cinture: “Non esistono i componenti di regolazione, perché sono troppo pesanti” e quindi bisogna rifornire di varie misure le scuderie. Il processo produttivo inizia dal taglio della cintura, poi si passa alla cucitura e infine al controllo di qualità, aspetto fondamentale per questo prodotto: inoltre in Sabelt è stato costruito un sistema per i test dinamici per la valutazione in autonomia degli impatti per i sedili e le cinture di sicurezza. “La Formula 1 ci impone la costante ricerca di tecnologia sempre più performante perché vuole prodotti leggeri che non inficino le performance della monoposto”, evidenzia il Vice Presidente di Sabelt. Dall’esperienza nel Circus, di recente l’azienda si è lanciata in un nuovo settore, quello dell’Aerospace e presto farà l’esordio anche nel trasporto aereo, a conferma che innovare ha sempre un ritorno economico. “Siamo fornitori della Nasa con le nostre cinture che servono per assicurare i rifornimenti per la Stazione Spaziale Internazionale, raggiunta dai cargo di Thales Alenia”, racconta Marsiaj. “Grazie alla nostra tecnologia abbiamo ridotto il peso delle cinghie da 110 chili ad appena 45: per la Nasa vuol dire poter caricare maggiori rifornimenti, risparmiando ulteriori spedizioni spaziali”. Nel settore del cargo commerciale, Sabelt sta rifornendo dei suoi prodotti sempre più leggeri e con un innovativo sistema di chiusura semplificato – non richiede l’impiego di due addetti, ma ne basta uno solo – alcuni player del settore, con importanti prospettive di sviluppo. Il business dell’azienda, che nei suoi 45 anni di storia è passata nelle mani degli americani di Trw per poi tornare di proprietà dei Marsiaj a fine Anni 90 ed essere riacquistata interamente solo nel 2015 dopo una breve parentesi in cui il Gruppo Brembo ne era diventato azionista, è per la maggior parte realizzato all’estero (circa il 90%) per effetto dei clienti finali delle case automobilistiche. Ora Sabelt ha pianificato importanti investimenti in Industria 4.0 per rispondere alle sfide della Digital Transformation: “Abbiamo deciso di investire 1,5 milioni di euro in progetti di digitalizzazione che comprendono soluzioni ERP e il sistema Electronic Data Interchange (EDI) per lo scambio di documenti tra diversi i sistemi informativi”, spiega il Vice Presidente illustrando i progetti dell’azienda per cavalcare la quarta rivoluzione industriale. Un obbligo anche per stare al passo con i clienti del calibro di Ferrari, con cui Sabelt condivide parte della Ricerca e Sviluppo per rispondere alla costante di richiesta di “velocità di consegna, flessibilità, qualità e produttività”. Ma sempre assicurando l’artigianato d’autore che ha conquistato il mondo.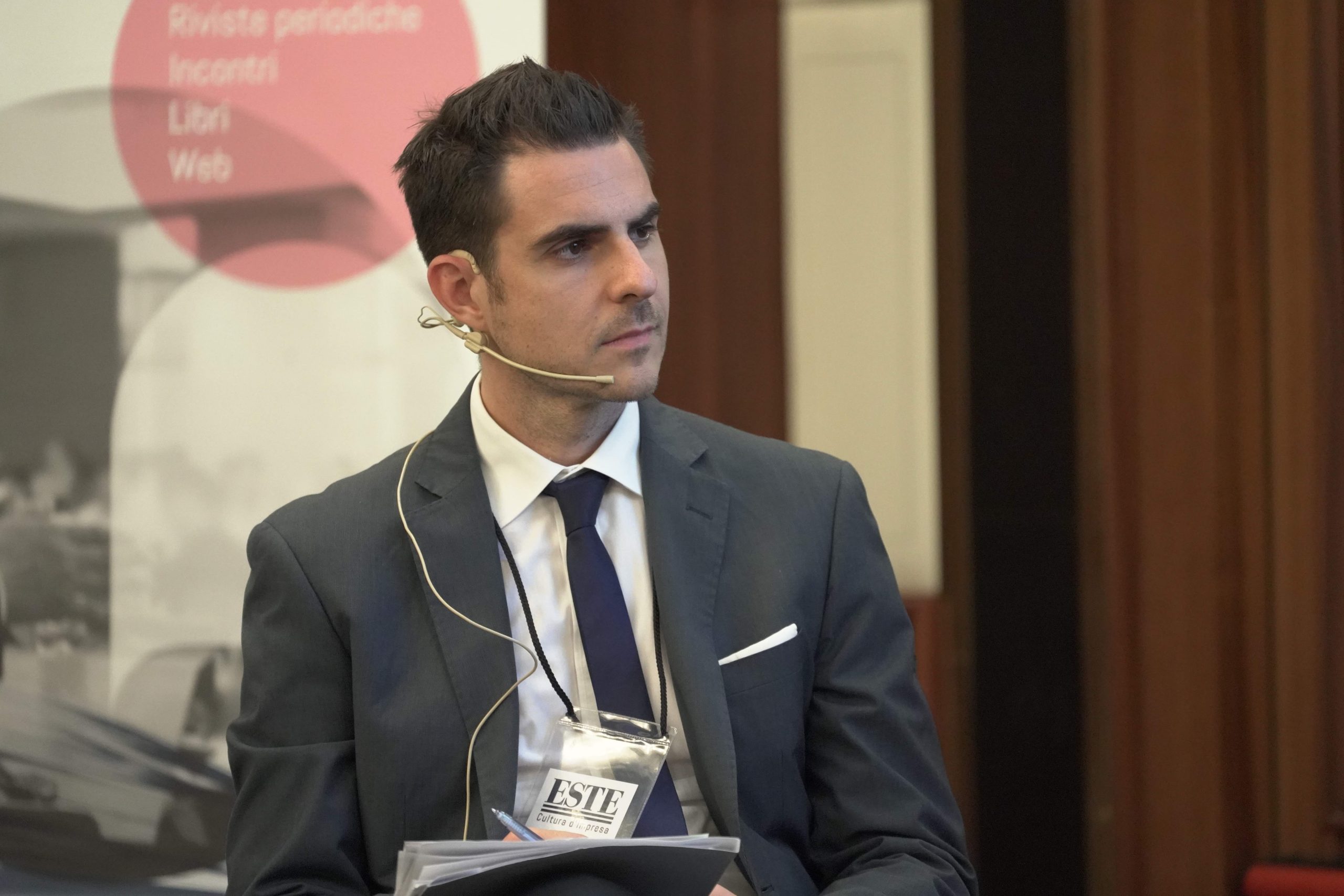
Dario Colombo, laureato in Scienze della Comunicazione e Sociologia presso l’Università degli Studi di Milano, è caporedattore della casa editrice Este. Giornalista professionista, ha maturato esperienze lavorative all’ufficio centrale del quotidiano online Lettera43.it dove si è occupato di Economia e Politica, e nell’ufficio stampa del Gruppo Ferrovie dello Stato Italiane.
Abarth, aerospace, Alfa romeo, Alpine Renault, automotive, Electronic Data Interchange, erp, Ferrari, Fiat, gestione documentale, industria 4.0, Massimiliano Marsiaj, Nasa, Produzione, Sabelt, Trw
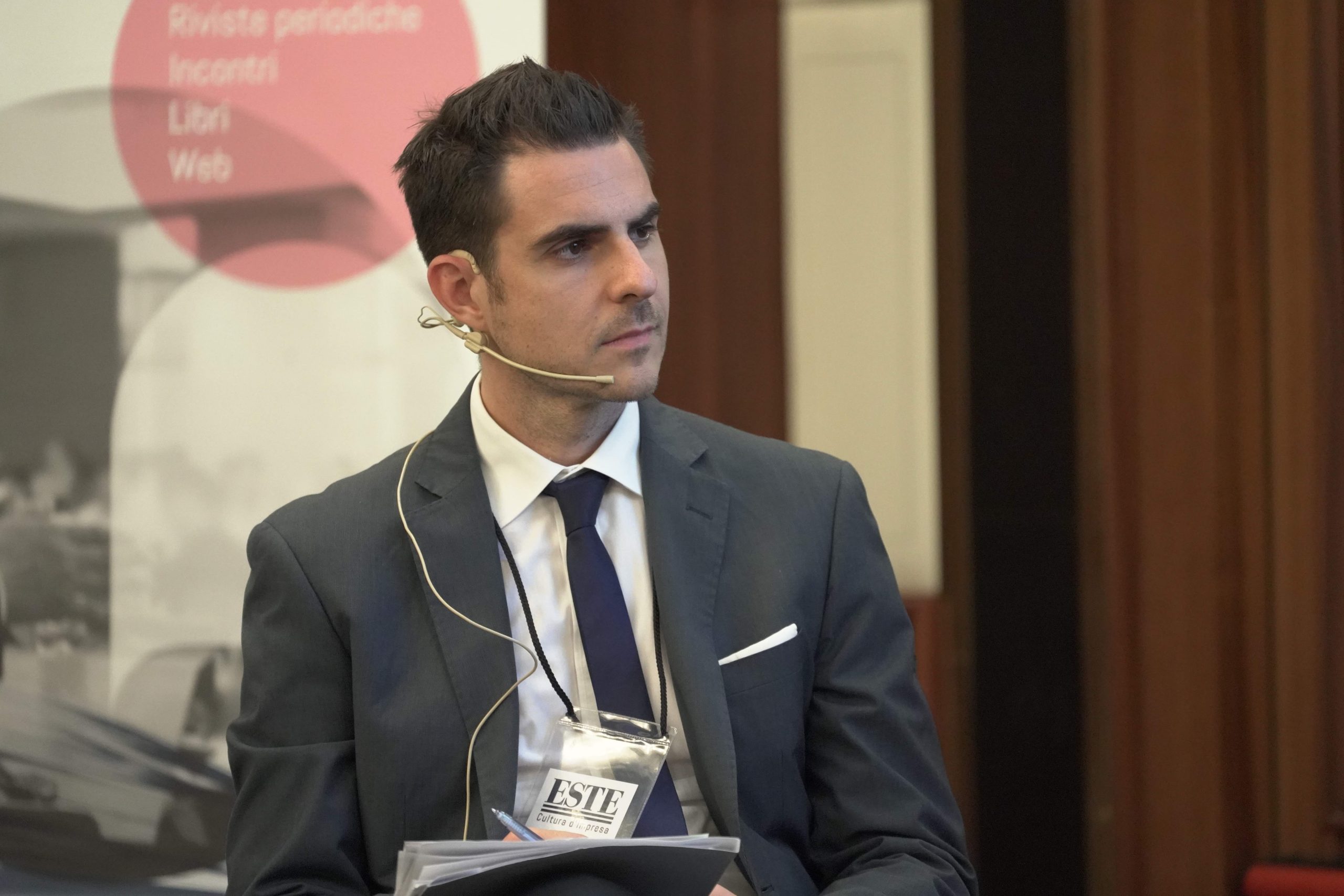