Materiali polimerici per la stampa 3D con tecnologia FDM
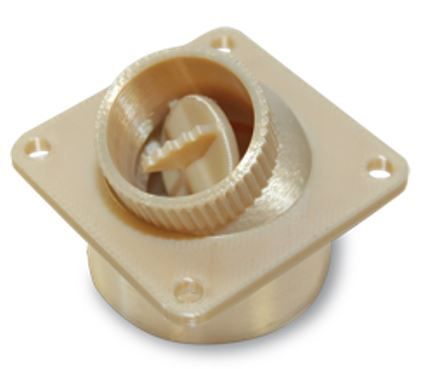
Con la stampa 3D si possono realizzare modelli concettuali, prototipi, utensili e parti finite. Le stampanti che utilizzano la tecnologia Fused Deposition Modeling sono oggi le più economiche e diffuse. Ciò ha portato a un importante sviluppo e alla commercializzazione di materiali con proprietà molto differenti. In questo articolo vengono illustrate le caratteristiche e i principali utilizzi dei diversi materiali
Laura Eleonora Depero*, Flavia Signorini*, Annalisa Zacco**
(*Laboratorio di Chimica per le Tecnologie, Università degli Studi di Brescia) (**SMART Solutions)
La manifattura additiva è una tecnologia di processo dove le parti sono create per strati depositati in successione. La ‘Fused Deposition Modeling’ (letteralmente: modellazione a deposizione fusa), a cui spesso si fa riferimento con l’acronimo FDM, è una tecnica additiva in cui ogni strato è formato da un “percorso” di materiale polimerico fuso, depositato da un ugello riscaldato. Il filamento di materiale termoplastico ha un diametro standard e viene fornito in bobine di varie dimensioni. Il principale vantaggio dell’FDM è la facilità di realizzare un prodotto partendo dal suo disegno virtuale, che può essere facilmente modificato direttamente sullo schermo. La validazione del prodotto può essere quindi realizzata in modo economico prima della produzione su grande scala.
Le stampanti che utilizzano la tecnologia FDM sono le più diffuse e a basso costo; ciò ha portato nel corso degli anni a un enorme sviluppo dei materiali impiegabili con differenti proprietà. Grazie a questa tecnologia è anche possibile stampare oggetti utilizzando materiali con differenti caratteristiche fisiche e funzionali, in modo da ottenere proprietà differenti nelle sue diverse parti. Fino a oggi, diversi tipi di materiali sono stati utilizzati solo per ottenere supporti ‘a perdere’ o, al più, la stampa di parti con diversi colori. La recente commercializzazione di filamenti di materiale termoplastico elastomerico (TPE) per stampanti FDM, rende possibile ottenere un oggetto ‘combinando’ due materiali con differente rigidità. I materiali termoplastici, quali ABS, PLA, PS, PET, Nylon, che hanno caratteristiche meccaniche (rigidezza, resistenza a trazione, resistenza a impatto) poco differenti, oggi possono essere combinati con elastomeri termoplastici con rigidezze anche di due ordini di grandezza inferiori, permettendo di ottenere pezzi stampati con proprietà meccaniche molto differenti.
Oltre alle applicazioni estetiche ed ergonomiche, la combinazione di un materiale termoplastico rigido e uno elastomerico, può avere numerose applicazioni funzionali.
I materiali
I materiali più utilizzati nelle stampanti FDM sono l’ABS e il PLA. Questi materiali hanno differenti caratteristiche e potenzialità e sono scelti in base alla funzione dell’oggetto da realizzare e alle proprietà desiderate. La tecnologia FDM utilizza le stesse termoplastiche impiegate nei processi produttivi tradizionali. In Figura 1 sono confrontati il modulo elastico e la durezza dei principali materiali utilizzati e nella tabella sono riportate la temperatura di estrusione, quella del piano riscaldato (se necessario) e i principali impieghi.
Figura 1 – Confronto dei moduli elastici e delle durezze dei principali materiali termoplastici utilizzati nella stampa additiva (grafici ottenuti utilizzando CES Selector, Granta Design)
TABELLA
Acrylonitrile Butadiene Styrene (ABS)
L’acrilonitrile-butadiene-stirene (ABS) ha formula chimica (C8H8· C4H6·C3H3N)n ed è un copolimero termoplastico molto utilizzato per creare oggetti leggeri e rigidi come tubi, parti di auto e giocattoli. È derivato dallo stirene polimerizzato insieme all’acrilonitrile in presenza di polibutadiene. Le proporzioni possono variare dal 15% al 35% di acrilonitrile, dal 5% al 30% di butadiene e dal 40% al 60% di stirene, come mostrato in Figura 2.
Figura 2
Lo stirene conferisce all’ABS una buona lavorabilità, l’acrilonitrile la rigidità e la resistenza termica e chimica, mentre il butadiene rende il materiale più tenace e resiliente, anche a basse temperature. L’ABS non ha grande resistenza ai raggi UV e non è idoneo al contatto con gli alimenti. Per questo motivo viene utilizzato per produrre oggetti rigidi e resistenti al calore.
La temperatura di estrusione è fra i 240-260°C. Richiede un piano riscaldato su cui essere stampato, in modo da rallentare la solidificazione e permettere alla base di aderire alla superficie ed evitare distacchi, evitando problemi di ritiro.
Acido polilattico (PLA)
Il PLA è un polimero termoplastico, tipicamente generato dalla fermentazione del mais o del grano. È inodore e igroscopico, quindi deve essere conservato in ambiente secco perché è fortemente idroscopico ed è idrosolubile a temperature maggiori di 70°C. La sua temperatura di estrusione è fra i 200°-230°C e non richiede un piano riscaldato poiché non ha problemi di ritiro.
Il PLA è più pesante e meno deformabile dell’ABS, ma ha un indice di ritrazione del 2-3% e si utilizza per realizzare oggetti grandi e lineari, laddove non siano richieste significative proprietà meccaniche.
Il FLEX PLA a differenza del PLA tradizionale, che è rigido e fragile, è flessibile, grazie alla percentuale di gomma contenuta, ed è ideale per costruire oggetti con buone proprietà di elasticità. È necessario stamparlo a basse velocità e a temperature di estrusione intorno ai 220-230°C.
Alcol polivinilico (PVA)
Come già accennato, per realizzare oggetti dalle forme particolari o che presentano sottosquadri sono necessari dei supporti, che possono essere creati con materiali appositi in stampanti a estrusore multiplo.
Il materiale più utilizzato per supporti è il PVA, alcol polivinilico, un polimero termoplastico, con una temperatura di transizione vetrosa di circa 85°C. Può essere estruso a temperature relativamente basse ed è idrosolubile, perciò ponendo l’oggetto finito in acqua il supporto si scioglie. Questo permette di ottenere facilmente oggetti che con tecnologie convenzionali non potrebbero essere realizzati in un unico pezzo.
Siccome a temperature maggiori di 200°C si decompone, al PVA sono aggiunti altri polimeri così da permetterne l’estrusione del filamento fra i 190 – 200°C.
Policarbonato (PC)
Il PC è un polimero termoplastico ottenuto dall’acido carbonico. Ha buona resistenza al calore e all’impatto, ma bassa all’intaglio. A differenza di molti polimeri termoplastici può sopportare grandi deformazioni plastiche senza rompersi. Ha una temperatura di transizione vetrosa di circa 150°C, ma per essere estruso e richiede temperature maggiori di 260°C. Ha problemi di adesione, quindi necessita di un piano riscaldato a circa 100°C. È il filamento ideale per la stampa di parti complesse, poiché non lascia sbavature; per questo è ampiamente usato nel settore automobilistico e aerospaziale.
www.rapidsol.org/polycarbonate.aspx
Il policarbonato assorbe l’umidità; quindi deve essere conservato in contenitori ermetici. Se ha assorbito acqua, il filamento risulta bianco e si formano bolle durante l’estrusione. Per non compromettere la qualità della stampa è necessario che sia sempre essiccato.
eSUN ha rilasciato un nuovo materiale, ePC 3D, un policarbonato semicristallino con ottime caratteristiche meccaniche e trasparenza, oltre a un ottimo livello di autoestinguenza. È però molto sensibile alla presenza di oli, i quali possono originare problemi e rotture.
Polietilentereftalato (PET);
Il PET è molto leggero e ha una buona resistenza all’impatto ed è quindi adatto per realizzare oggetti leggeri. Ha buona adesione alla superficie di stampa, quindi non necessita di un piano riscaldato. La sua temperatura di transizione vetrosa è di circa 60°C, mentre quella di estrusione di circa 260°C; se si estrude a temperature troppo alte si possono avere oggetti con superfici filamentose. Non presenta particolari difficoltà di utilizzo e può essere utilizzato per realizzare contenitori di liquidi e alimenti.
Il produttore olandese FormFutura ha sviluppato una nuova formula di PET, chiamato HDglass, con cui si ottengono oggetti molto trasparenti. HD significa ‘heavy duty’ poiché è un materiale flessibile ed estremamente resistente; possiede le stesse qualità di forza, durata e resistenza al calore degli altri filamenti di PET presenti sul mercato, ma consente al 90% della luce visibile di passare attraverso, con solo l’1% di distorsione.
http://www.stampa3dstore.com/
High Impact PolyStyrene (HIPS)
L’HIPS è costituito da polistirene e da gomma stirene-butadiene dispersa. La presenza delle particelle di elastomero conferisce un maggiore allungamento a rottura, una maggiore resistenza all’impatto e rende gli oggetti realizzati più opachi. Viene estruso a temperature di circa 230 – 250°C e necessita di un piano riscaldato a 90 – 110°C. Si scioglie completamente in limonene, quindi può essere utilizzato nel secondo estrusore per la realizzazione di supporti; generalmente viene abbinato all’ABS; è utilizzato anche per stampe tecniche, coperchi per macchine industriali dove non sia richiesta resistenza ai raggi UV, creazione di box con resistenza agli urti (es. contenitori CD) e anime per stampaggio in terra.
Può presentare problemi di delaminazione tra gli strati. In commercio esistono materiali che possono essere successivamente lavorati tramite incollatura, verniciatura o sabbiatura (es. Z-HIPS).
FormFutura ha inoltre introdotto una versione di HIPS chiamato EasyFil HIPS che è un po’ più morbido e flessibile rispetto ai filamenti tradizionali e quindi più semplice da stampare.
Nylon
Il Nylon è il nome commerciale di un polimero a base poliammidica. A differenza dell’ABS e del PLA è meno fragile e resiste bene allo strappo; ha un grande allungamento a rottura (circa 300%), buona resistenza all’abrasione e buona resilienza. Grazie alle sue proprietà autolubrificanti è utilizzato per la realizzazione di ingranaggi. Il Nylon può avere però deformazioni e ritiri maggiori dell’ABS, quindi necessita di un piano riscaldato per essere stampato; inoltre è un materiale molto fibroso, perciò la velocità di stampa è limitata, poiché potrebbe compromettere la realizzazione dell’oggetto. La temperatura di estrusione del Nylon è compresa fra 235° e 260°C. I produttori delle bobine suggeriscono una specifica temperatura di estrusione che dipende dai polimeri con i quali è addittivato per migliorare le sue caratteristiche.
Polimetilmetacrilato (PMMA)
Il PMMA, altrimenti conosciuto col nome commerciale di Plexiglass, è un materiale antiurto con una resistenza meccanica superiore all’ABS e una notevole resistenza agli agenti atmosferici e chimici, ma è igroscopico. Viene generalmente estruso a temperature di circa 270°C per le bobine essiccate, mentre per le bobine che hanno assorbito umidità la temperatura di estrusione è di circa 235°C; necessita di piano riscaldato. La lavorazione a temperatura più bassa non influisce negativamente sull’aspetto del prodotto finito, ma ne limita la resistenza meccanica a causa della minore adesione tra gli strati. La sua caratteristica dovrebbe essere la grande trasparenza, simile al vetro, che però è difficile da ottenere.
Il PMMA possiede un ottimo grado di biocompatibilità con i tessuti umani. In ortopedia è usato come ‘cemento’ per fissare impianti, per rimodellare parti di osso perdute o ‘riparare’ vertebre fratturate.
Il PMMA può essere caricato con polveri di Alluminio, ottenendo un filamento grazie al quale si ottengono oggetti resistenti e rigidi, anche se la finitura superficiale non è ottima. Viene estruso a 225°–240°C ed è necessario un piano riscaldato. L’alluminio conferisce un aspetto luminoso, tant’è che questo filamento viene spesso commercializzato con il nome di PMMA Glitter.
Polyphenilsulfone (PPSF/PPSU)
Il PPSF/PPSU garantisce la massima resistenza al calore rispetto a tutte le termoplastiche FDM, buona forza meccanica e resistenza al petrolio e ai solventi. Può essere sterilizzato con i raggi gamma e in autoclave. Le incredibili proprietà di questo materiale ampliano le possibilità di utilizzo della stampa 3D, velocizzando lo sviluppo dei prodotti, aumentando la sicurezza dei test e riducendo i rischi. Il polifenilsulfone è ideale per la realizzazione di prototipi che debbano resistere a condizioni estreme. La sua ottima resistenza alle alte temperature e agli agenti chimici lo rende un ottimo materiale per test funzionali, ideale per applicazioni in ambienti caustici e soggetti a temperature elevate (fino a 170°C). Il Polifenilsulfone, grazie alle sue caratteristiche tecniche e meccaniche, può essere utilizzato per la produzione di particolari definitivi di automobili e per i settori nautico, aeronautico e aerospaziale.
Poliuretano termoplastico (TPU)
Il TPU ha grande elasticità, resistenza al taglio e resiste al grasso e alle abrasioni. Ha molte applicazioni nella costruzione di pannelli per automotive, rotelle, utensili elettrici e dispositivi medici. Non emette fumi tossici o odori fastidiosi durante l’estrusione e viene stampato a temperature tra 240° e 260 °C.
Negli ultimi anni le aziende produttrici di filamenti stanno modificando i materiali già in commercio per ottenere particolari performance. Ne riportiamo alcuni a titolo di esempio.
Laybrick
Questo materiale è composto da una miscela di gesso macinato finemente e copoliestere e permette di ottenere oggetti che all’apparenza risultano simili al gesso. Questa caratteristica lo rende idoneo per creare plastici e modelli di architettura. È un materiale con scarsa deformabilità, quindi non necessita di piano riscaldato; viene estruso a temperature fra 170°–210°C. Utilizzando velocità di stampa contenute è possibile ottenere una maggiore adesione tra gli strati e oggetti più resistenti. Si possono realizzare sia superfici levigate che ruvide ed è possibile dipingere l’oggetto a stampa ultimata.
http://3dprintingforbeginners.com/3d-printing-materials-bendlay-laywood-laybrick/
Ninjaflex
Questo materiale è costituito da un elastomero termoplastico (TPE) che permette di realizzare oggetti flessibili con ottime proprietà elastiche: si può allungare e piegare, riprendendo poi la forma originale dell’oggetto. Inoltre è molto resistente all’abrasione e ha un’eccellente adesione al piano di stampa e tra gli strati.
Viene estruso a temperature fra 210°–230°C e per migliorare ulteriormente l’adesione si utilizza un piano riscaldato a circa 30°C. Deve essere stampato a velocità non troppo elevate.
https://www.matterhackers.com/store/3d-printer-filament/ninjaflex
Laywood
Laywood è una miscela di fibre, ottenute da legno riciclato, miscelate con un polimero termoplastico con caratteristiche simili al PLA. Si deforma poco e non richiede un piano riscaldato per essere stampato. Viene estruso a temperature comprese tra 180°-250°C e a seconda della temperatura di estrusione ha un diverso colore: a 185°C è marrone chiaro mentre a 250°C è molto più scuro. Grazie a questa caratteristica, è possibile ricreare la colorazione tipica del legno.
Gli strati hanno grande adesione tra di loro e difficilmente sono distinguibili nell’oggetto finito. Grazie all’elevata percentuale di fibra contenuta nei filamenti (40% o superiore) gli oggetti realizzati sembrano di legno e ne hanno lo stesso odore; è inoltre possibile eseguire dei trattamenti di finitura superficiale tipici del legno, come la levigatura. Il filamento è molto fragile e si rompe facilmente, quindi bisogna fare attenzione quando lo si inserisce nell’estrusore.
www.technikneuheiten.com/laywood-ermoglicht-3d-druck-mit-holz/
Glass
Il Glass è un copoliestere termoplastico miscelato con fibra di vetro utilizzato per realizzare elementi traslucidi con alta resistenza a trazione, elevata resistenza alle alte temperature e all’abrasione. Permette di ottenere oggetti duri con un’elevata coesione tra gli strati. A seconda della tipologia di copoliestere col quale viene creato, può essere estruso a temperature che variano fra 190° e 230°C.
Carbonfil
Il Carbonfil, prodotto dalla FormFutura, è un filamento molto leggero rinforzato con il 20% di fibre di carbonio relativamente lunghe. Si ottengono oggetti rigidi e dalla grande resistenza all’impatto, con una buona stabilità dimensionale e resistenza al calore. Viene estruso fra 240°e270°C senza la necessità di un piano riscaldato. Gli strati hanno grande adesione tra loro e permettono di realizzare oggetti con un’alta definizione. È impiegato nell’industria automobilistica.
www.formfutura.com/
PEI (polietermide)
Questo polimero amorfo, chiamato commercialmente Ultem, presenta una notevole combinazione di proprietà termiche, meccaniche ed elettriche oltre a un basso livello di infiammabilità, che determina una scarsa emissione di fumi durante la combustione. Queste caratteristiche rendono la resina estremamente adatta per l’utilizzo in apparecchiature elettrico/elettroniche, oltre che per componenti strutturali che richiedono alta resistenza e rigidità in presenza di temperature elevate.
Ottenuti con questo polimero sono commercializzati speciali filamenti con altissime prestazioni. Ad esempio l’Ultem 9098 prodotto dalla Stratasys ha proprietà termiche, meccaniche e chimiche eccezionali ed è certificato per il suo utilizzo anche negli Airbus: si producono parti che sono più leggere e incredibilmente resistenti, ma anche compatibili con fuoco. Il materiale infatti non favorisce incendi e, nel caso, non rilascia fumo dannoso e/o tossico (classificazione FST).
www.stratasys.com/it/materiali/fdm/ultem-9085
Conclusioni
Grazie allo sviluppo di nuovi materiali, sempre più opportunità sono offerte oggi dalla stampa 3D con tecnologia FDM. Dal momento che il prezzo delle stampanti FDM è crollato, il suo uso si è rapidamente diffuso anche negli uffici, nelle istituzioni educative e nel settore privato.
La tecnologia FDM si può utilizzare con materiali molto differenti, permettendo lo sviluppo di sempre nuovi prodotti. Per questo, la stampa 3D viene da molti considerata come portatrice di una nuova rivoluzione industriale, in grado di offrire vantaggi in tutto il processo di creazione del prodotto, dal design iniziale alla finale produzione.
Comprendere i requisiti necessari affinché il prodotto abbia le caratteristiche richieste è fondamentale nella scelta del materiale. D’altra parte, ogni materiale introdotto sul mercato apre nuovi campi di applicazione del processo FDM. Enormi passi avanti si sono fatti in pochi anni nello sviluppo di nuovi filamenti a base polimerica e oggi le stampanti 3D sono già in grado di utilizzare colori e materiali multipli. Lo sviluppo di nuovi materiali permetterà certamente in futuro di ottenere prodotti con funzionalità fino a oggi sconosciute. In particolare, ci sono ancora pochi esempi di materiali metallici e ceramici depositati con tecniche FDM, ma già molto promettenti e le prospettive applicative future della stampa 3D saranno probabilmente limitate solo dalla nostra creatività.