Industria 4.0 e innovazione robotica, la collaborazione uomo-macchina
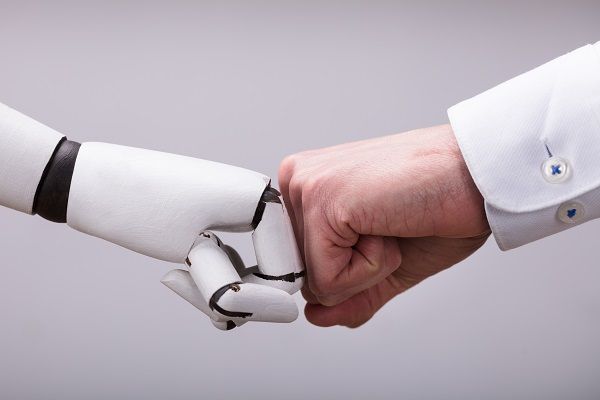
I cambiamenti in atto nei processi produttivi sono attualmente guidati dal paradigma emergente di Industria 4.0 e riguardano prevalentemente le modalità con cui gli attori di tali processi interagiscono tra loro nella realtà industriale.
I concetti chiave di tali cambiamenti, solitamente declinati in inglese, sono: Internet of Things (IoT), Cyber Physical System (CPS), Big data, Collaborative Robot (cobot), ecc. In realtà essi rappresentano una naturale evoluzione di sviluppi tecnologici industriali precedenti ma rendono necessarie nuove forme di interazione tra uomini e macchine, o meglio, tra esseri umani e sistemi artificiali intelligenti.
La Robotica collaborativa, da oggetto di ricerca ormai divenuta opportunità di business per le imprese, sviluppa gli aspetti legati alla cooperazione tra operatori e robot, garantendo la sicurezza dei primi e cercando di estendere le opportunità di utilizzo dei secondi.
Evoluzione della robotica
Quando George Devol nei primi Anni 60 installò i primi robot in General Motors chiamò la sua azienda Unimation, da “universal automation”, testimoniando le aspettative di quel periodo in macchine intelligenti e universali, in grado di aiutare i lavoratori in ogni campo, proprio come i robot dei romanzi di Asimov, che hanno influenzato i primi passi della robotica.
Per molti anni, tuttavia, i robot hanno trovato una giustificazione economica solo in fabbrica e anzi, per poter essere competitivi, hanno richiesto una specializzazione di struttura meccanica e sistema di controllo rispetto alle particolari applicazioni a cui sono stati adibiti.
Le prestazioni sempre più spinte richieste ai robot industriali e le aumentate esigenze di sicurezza hanno fatto sì che l’intera cella automatizzata, se non l’intero impianto, fossero costruiti intorno al robot lasciando poco spazio, sia in senso fisico che metaforico, per la presenza di un operatore umano.
Tuttavia negli anni più recenti robot avanzati sono usciti dalle fabbriche, sono diventati più autonomi e hanno conquistato i campi più diversi, dalla medicina all’intrattenimento, dalle applicazioni domestiche all’assistenza e riabilitazione, tanto che si sono delineati concetti quali il personal robot, la robotica indossabile, i robot umanoidi, ecc.
Con l’affermarsi della Robotica collaborativa, queste due traiettorie di sviluppo così differenti si stanno ricomponendo e anche i robot industriali sono ora in grado di interagire in sicurezza con gli esseri umani: si assiste a una ‘liberazione’ dei robot che escono dalle gabbie e lavorano insieme agli operai nelle Smart factory.
I robot diventano collaborativi
I cobot sono robot industriali pensati per lavorare insieme all’uomo in sicurezza, senza barriere o gabbie protettive a dividerli. Ciò è reso possibile da una recente normativa internazionale del 2016, la ISO/TS 15066 che dettaglia le caratteristiche dei robot e le modalità operative affinché l’interazione possa avvenire in sicurezza. Sono solitamente distinti tre livelli di cooperazione crescente:
• aree di lavoro sicure: attraverso un’apposita sensorizzazione dello spazio di lavoro, il robot rallenta o si arresta (non in emergenza) all’avvicinarsi dell’operatore; questa modalità di lavoro si adatta per quelle lavorazioni in cui qualsiasi contatto deve essere impedito in quanto potenzialmente pericoloso: essa è quindi utilizzata con robot pesanti o rigidi e veloci e lo spazio di lavoro viene condiviso solo occasionalmente;
• aree di lavoro condivise tra operatore e robot: questi lavorano nella stessa area e sono possibili contatti volontari o accidentali. In questa modalità operativa è consentita una coesistenza di uomo e robot in completa protezione per l’operatore; pertanto lo spazio di lavoro può essere condiviso in modo continuativo per l’esecuzione di lavorazioni ‘leggere’ o svolte a bassa velocità dal robot;
• esecuzione di compiti con interazione fisica tra operatore e robot: attraverso il controllo della forza sviluppata dal robot, questo può cooperare con l’operatore anche attraverso la manipolazione di uno stesso oggetto; oppure il sistema di controllo del robot può compensare gli effetti gravitazionali e l’operatore umano può agevolmente spostare il dispositivo terminale nel campo di lavoro, per esempio in fase di programmazione.
Per garantire il livello di sicurezza previsto dalla normativa sono predisposti molteplici accorgimenti, quali per esempio: la ridondanza (di sensori, dispositivi, di controllo) per ovviare a eventuali guasti, l’utilizzo di pelle capacitiva o di sensori di prossimità per monitorare o prevenire il verificarsi di urti, l’utilizzo di sensori di forza e di coppia per limitare le forze di contatto, ecc.
Inoltre per assicurare la protezione degli operatori in caso di urti o contatti i cobot hanno membri leggeri e talvolta ricoperti di materiale apposito, hanno giunti arrotondati o plastificati e sono il più possibile ergonomici, a misura d’uomo; inoltre non ci sono motori, cavi, componenti meccanici o elettronici esposti.
L’articolo integrale è pubblicato sul numero di Marzo-Aprile 2019 di Sistemi&Impresa.
Per informazioni sull’acquisto di copie e abbonamenti scrivi a daniela.bobbiese@este.it (tel. 02.91434400)