Andare oltre il paradigma 4.0, la digitalizzazione della filiera

Per parlare di quarta rivoluzione industriale è necessario chiarire alcuni punti chiave che ruotano attorno a questa definizione. L’espressione “rivoluzione industriale”, infatti, coincide con l’introduzione di un’innovazione di prodotto o di processo che modifica radicalmente la produttività e quindi l’output a disposizione del consumatore a parità di risorse consumate. In passato lo scenario è stato rivoluzionato dalla macchina a vapore, dall’avvento del taylorismo, così come anche dall’informatica e dall’elettronica. Oggi il ruolo di innovatore è ricoperto dall’automazione industriale.
“Industria 4.0”, come è noto, è un termine coniato per la prima volta in Germania, dove un gruppo di lavoro dedicato – presieduto da Siegfried Dais, Manager di Bosch GmbH, e da Henning Kagermann, membro dell’Executive Board di Acatech (Accademia tedesca delle Scienze e dell’Ingegneria) – presentò al Governo federale una serie di raccomandazioni per la sua implementazione. L’8 aprile 2013, in occasione della Fiera di Hannover, fu diffuso il report finale del gruppo di lavoro: un progetto per lo sviluppo del settore Manifatturiero che avrebbe dovuto riportare l’industria del Paese a un ruolo leader nel mondo. Si è rivelato essere il capostipite di numerose iniziative europee ispirate proprio da questa iniziativa.
Macchine intelligenti per la Smart production
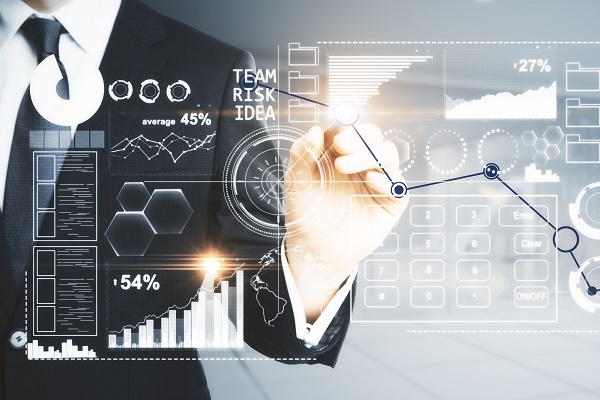
Ciò che definisce la quarta rivoluzione industriale è il fatto che le macchine e i prodotti acquisiscono due caratteristiche fino a ora assenti: diventano intelligenti e connesse, ossia sono in grado di comunicare tra loro attraverso connessioni di Rete. Se nella terza rivoluzione industriale le macchine ‘semplicemente’ automatizzavano il lavoro dell’uomo in maniera ripetitiva, con la quarta iniziano a comportarsi come l’essere umano.
L’uomo elabora attraverso il cervello le informazioni che provengono dai cinque sensi e genera risposte o azioni coerenti; allo stesso modo le macchine 4.0 ricevono input dal mondo esterno attraverso sensori sempre più sofisticati ed essendo connessi, in maniera più o meno estesa attraverso Internet, possono inviare tali informazioni a un ‘cervello’ che rappresenta un modello virtuale del sistema, il cosiddetto digital twin. Questo può essere a bordo macchina o dall’altra parte del mondo; può comprendere una sola macchina o macchine di molteplici stabilimenti. In ogni caso, i parametri che provengono dal campo vengono elaborati, simulando in frazioni di secondo diversi possibili scenari, e generano un output consistente con determinate funzioni obiettivo. L’output viene poi inviato nuovamente alle macchine. Esattamente come fa il cervello umano!
Si parla a tal proposito di ‘autonomous robots’, macchine autonome, connesse tra loro e con il mondo esterno, in grado di rimpiazzare e di affiancare l’uomo nello svolgimento non solo dei compiti ripetitivi, ma anche delle mansioni sempre più complesse, grazie alla capacità di prendere decisioni al mutare delle condizioni al contorno.
Quindi, non ci sono solo mulettisti nei magazzini rimpiazzati da robot che portano in giro pallet o scaffalature, o trasportatori per la distribuzione delle merci sostituiti da droni o da veicoli a guida autonoma: anche gli addetti ai call center o che svolgono attività di assistenza sono destinati a essere sostituiti da Intelligenze Artificiali come Siri, Ok Google o chatbot. È di giugno 2018 la notizia che Ikea ha ‘assunto’ Vera, un robot lanciato nel 2017 da una startup russa, in grado di svolgere 1.500 colloqui di lavoro al giorno…
Per continuare a leggere l’articolo, leggi il numero di Novembre-Dicembre 2018 di Sistemi&Impresa.
Per informazioni sull’acquisto di copie e abbonamenti scrivi a daniela.bobbiese@este.it (tel. 02.91434400)
digitalizzazione, industria 4.0, smart production, supply chain