Il binomio artigianato-industria nella nuova fabbrica di Balocco
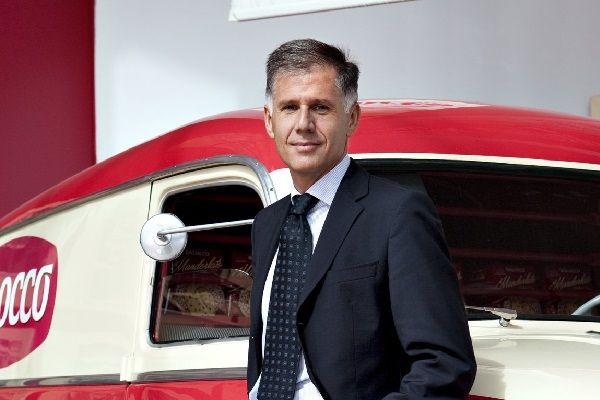
Tecnologia e automazione, senza dimenticare qualità e tradizione. Sono gli ingredienti essenziali della ricetta più importante di Balocco, l’azienda dolciaria piemontese diventata celebre per il mandorlato e oggi secondo player a livello nazionale anche nel mercato della prima colazione, dietro solo al colosso Mulino Bianco.
Un’evoluzione che nell’ultimo decennio ha visto l’impresa nata nel 1927 da una piccola pasticceria artigianale di Fossano – 25mila abitanti in provincia di Cuneo – crescere al ritmo di 1 milione di euro al mese fino a quasi raddoppiare il fatturato, dai 103 milioni del 2008 (l’anno del fallimento di Lehman Brothers) ai 190 milioni del 2018.
Allo scoppio della crisi economica mondiale l’azienda guidata dall’Amministratore Delegato Alberto Balocco (nella foto), nipote di quel Francesco Antonio che la fondò quasi un secolo fa, si è fatta trovare preparata, con i conti in ordine e le idee chiare.
Così, mentre molte aziende si trovavano alle prese con problemi finanziari, industriali o commerciali, a Fossano si dava il via a un massiccio piano di investimenti che in 10 anni, tra forni di cottura di ultima generazione e sistemi automatici di impasto e confezionamento, ha portato Balocco a investire più di 50 milioni in tecnologia.
“La nostra è stata un’iniezione costante di automazione”, spiega l’Amministratore Delegato, entrato in azienda nel 1990 insieme con la sorella Alessandra, oggi Responsabile del Marketing. “Ogni anno investiamo una parte rilevante dei nostri ricavi e di conseguenza ogni anno diventiamo un po’ più efficienti e un po’ più competitivi”.
Collaborazione uomo-macchina
La manifattura dolciaria, in cui nel Dopoguerra papà Aldo aveva avviato la produzione industriale di panettoni, pandori e colombe pasquali, si è trasformata in una fabbrica 4.0 altamente automatizzata. Uno stabilimento ipertecnologico dove le operazioni più ripetitive sono state gradualmente affidate ai robot, più efficienti e performanti e sicuramente meno esposti al rischio burnout lavorativo. Il risultato è “un processo produttivo più rigido, forse, ma molto più rigoroso”, spiega Balocco, “dove la qualità è garantita da un software che lo replica in maniera sempre uguale”, senza le oscillazioni che contraddistinguono l’attività artigianale. “Oggi quasi tutte le operazioni che potevano essere automatizzate sono state robotizzate”. Eppure, contrariamente a quello che si potrebbe pensare, il crescente utilizzo di robotica non ha portato a una riduzione dell’organico, che invece è cresciuto di oltre il 30%. L’automazione ha messo in moto un circolo virtuoso che, moltiplicando le tonnellate di prodotto per ora lavorata, ha abbattuto drasticamente l’incidenza del costo del lavoro. Una competitività che si riversa sui prezzi e di conseguenza sulle vendite, portando l’azienda a produrre sempre di più. “Anche se ci sono meno addetti per turno, oggi si fanno più turni e di conseguenza il lavoro non diminuisce, anzi aumenta”. E con esso anche il numero di dipendenti. Per la campagna natalizia 2018 l’organico del sito di Fossano è arrivato a 400 unità, cifra che sale fino a 480 se si contano anche i lavoratori interinali e le cooperative.Senso di appartenenza dei dipendenti
Nella fabbrica 4.0 è cambiato anche il modo di lavorare: “In passato si trattava prevalentemente di fare un lavoro di manovalanza”, spiega l’Amministratore Delegato. “Adesso si tratta soprattutto di controllare i processi. È più gratificante e la qualità del lavoro ne guadagna”. La conferma arriva direttamente dai suoi dipendenti. Per il secondo anno consecutivo, infatti, Balocco è tra le prime cinque aziende del largo consumo in cui si lavora meglio secondo l’indagine realizzata dalla società tedesca indipendente Statista che ha interpellato i lavoratori di oltre 2mila imprese italiane con più di 250 dipendenti. La ragione? “Tra i nostri dipendenti c’è una grande percezione del contributo al successo dell’azienda. Chi lavora in un’azienda che si espande, che installa nuovi impianti, che investe in ricerca e sviluppo e che migliora gli ambienti di lavoro, si sente partecipe di questo successo ed è maggiormente motivato a fare bene. Si crea un forte senso di appartenenza che innesca una spirale virtuosa”.
L’articolo integrale è pubblicato sul numero di giugno di Sistemi&Impresa.
Per informazioni sull’acquisto di copie e abbonamenti scrivi a daniela.bobbiese@este.it (tel. 02.91434400)
Alberto Balocco, artigianato-industria, Balocco, Collaborazione uomo-macchina, Fabbrica 4.0