L’innovazione industriale è solo all’inizio
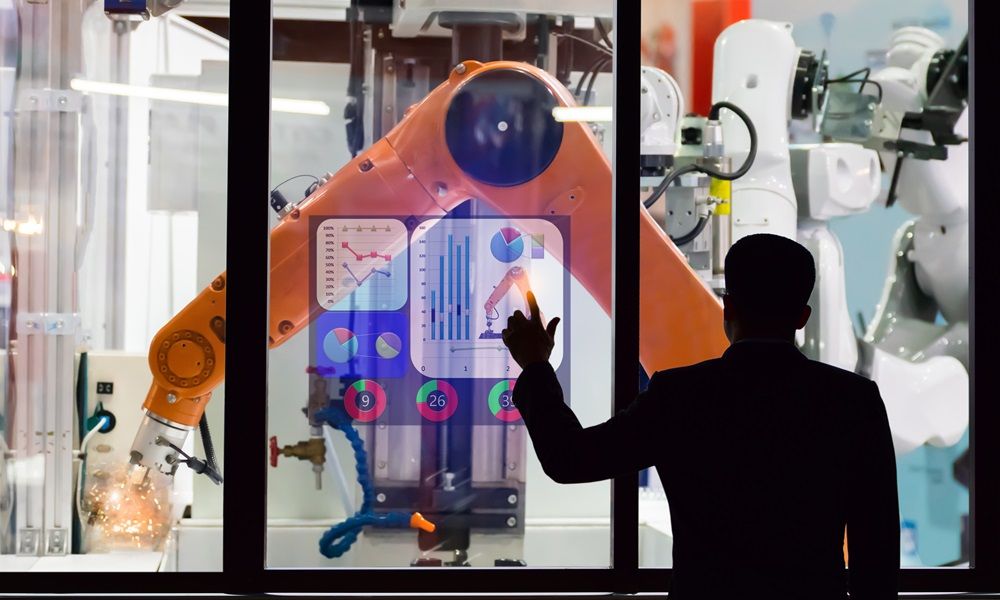
Negli ultimi anni molte imprese italiane hanno modernizzato il loro parco macchine, senza però sfruttare a pieno le potenzialità della Quarta Rivoluzione industriale. La causa non sembrerebbe l’insufficienza di incentivi economici e governativi, ma una mancata comprensione del concetto di “Industria 4.0” e di scarsità di competenze adeguate all’interno delle organizzazioni. È quanto emerge dalla ricerca dal titolo Il fenomeno Industria 4.0 nelle aziende manifatturiere italiane: tendenze, barriere e contromisure realizzata da Liuc Business School per la società di consulenza e certificazione Icim Group, il cui obiettivo è capire come la Manifattura italiana abbia affrontato, negli anni successivi all’investimento, l’implementazione delle tecnologie 4.0 acquisite, analizzando in particolare quali siano le principali tendenze e barriere evolutive.
Il termine “Industria 4.0” è stato utilizzato per la prima volta nel 2011 alla Fiera di Hannover, in Germania, come ipotesi di un progetto di investimenti in infrastrutture, scuole, sistemi energetici, enti di ricerca e aziende per ammodernare il sistema produttivo tedesco e riportare la Manifattura ai vertici mondiali. In Italia il Piano nazionale Industria 4.0 2017-2020 è stato presentato invece ‘solo’ a settembre 2016, dall’allora Ministro dello Sviluppo Economico Carlo Calenda, e ha previsto una serie di misure organiche e complementari in grado di favorire gli investimenti per l’innovazione e la competitività.
Aumentare il valore dei processi produttivi
Come riporta l’introduzione del Rapporto, la Quarta Rivoluzione industriale è una continuazione della Terza Rivoluzione (anche nota come “Rivoluzione digitale” e sviluppatasi negli Anni 70 e 80, caratterizzata dall’introduzione del computer e delle tecnologie informatiche che hanno così permesso l’automazione dei processi produttivi e portato all’evoluzione della tecnologia dell’informazione e della comunicazione), ma che si concentra sulla digitalizzazione e sull’integrazione di tecnologie avanzate per migliorare la produttività, l’efficienza e la qualità della Produzione.
L’obiettivo dell’Industria 4.0 è, infatti, aumentare il valore generato dai processi produttivi in termini di efficienza, qualità, flessibilità, sostenibilità e sicurezza, grazie all’integrazione di nove pilastri tecnologici individuati e descritti da Boston Consulting Group (dall’Internet of Things al Big data analytics; dalla Manifattura additiva alla Realtà aumentata e simulazione) che consentono di raggiungere l’automazione industriale, l’integrazione delle risorse all’interno della fabbrica e l’attuazione di processi decisionali guidati dai dati.
“Alla vigilia della revisione degli incentivi per la digitalizzazione ci sembrava importante mettere a disposizione il patrimonio di esperienze raccolto in cinque anni di attività connesse all’attestazione di beni Industria 4.0. Abbiamo condiviso i nostri dati per indagare con maggiore dettaglio quali tecnologie siano state preferite dalle imprese, per quali utilizzi, con quali obiettivi”, ha commentato Paolo Gianoglio, Direttore Innovazione, Sviluppo e Relazioni Associative di Icim Group e Responsabile del Progetto Industria 4.0. “Nei prossimi anni la sfida della digitalizzazione si incrocerà con quella della sostenibilità, la cosiddetta ‘Twin transition’ che l’Europa ci chiede per rispondere a criteri di competitività che non compromettano l’impegno per combattere il cambiamento climatico. Con la ricerca commissionata a Liuc crediamo di aver offerto un contributo significativo per le decisioni dei prossimi anni”.
Fare strada all’economia dei dati
La ricerca rivela che le imprese italiane, dopo gli investimenti 4.0, hanno ottenuto risultati positivi come maggior produttività, maggiore controllo dell’impianto produttivo e miglioramento delle condizioni di lavoro. Tuttavia, la decisione di investire è stata principalmente legata ai vantaggi economici (75%), mentre solo il 25% ha citato una cultura digitale e l’ambizione di abbracciare la Quarta Rivoluzione industriale. Le barriere all’innovazione includono la mancanza di comprensione dell’Industria 4.0 (67%), resistenza al cambiamento (75%), complessità nell’integrare nuovi sistemi (83%) e difficoltà a trovare partner validi (57%). L’analisi evidenzia anche uno scarso utilizzo dei dati generati dai nuovi impianti e sottolinea la necessità di una maggiore consapevolezza delle potenzialità dell’economia dei dati nel settore manifatturiero.
“I dati sono oggi da considerarsi un vero e proprio asset strategico. Tuttavia, la scarsa conoscenza dei pilastri tecnologici 4.0 e dei processi basati sui dati porta le imprese a non utilizzare tali informazioni o a utilizzarne solo una parte per analisi di tipo descrittivo, non applicando analitiche prescrittive o predittive che ne potenzino il valore e guidino meglio le decisioni, proteggendo poco l’aspetto di privacy e tutela del dato stesso, con bassi investimenti in cybersecurity”, ha evidenziato Violetta Giada Cannas, Ricercatrice della Liuc Business School e curatrice dello studio. Per cambiare lo scenario occorre che tutti gli attori della filiera, a partire da università e Competence center, si impegnino per favorire l’evoluzione del settore manifatturiero verso l’economia dei dati, adottando politiche incentivanti e riconoscendo la potenzialità che l’utilizzo dei dati può offrire (come già efficacemente sperimentato in altri settori come banche, assicurazioni e Social media).
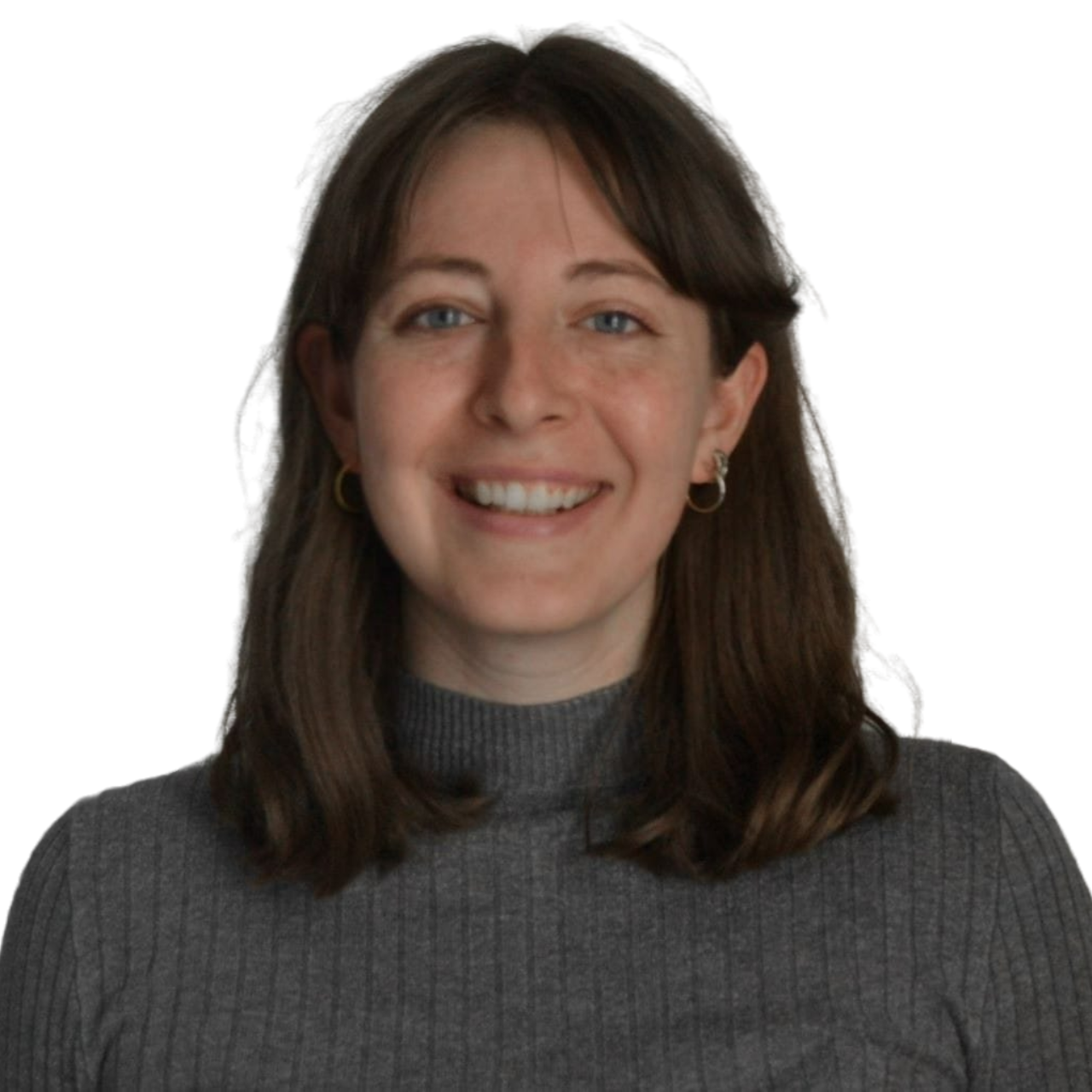
Classe 1996, Martina Midolo scrive di cultura d’impresa e si occupa di social media. Per FabbricaFuturo conduce il podcast Storie dell’Italia che produce.
digitalizzazione, gestione dati, Icim Group, industria 4.0, Liuc business school
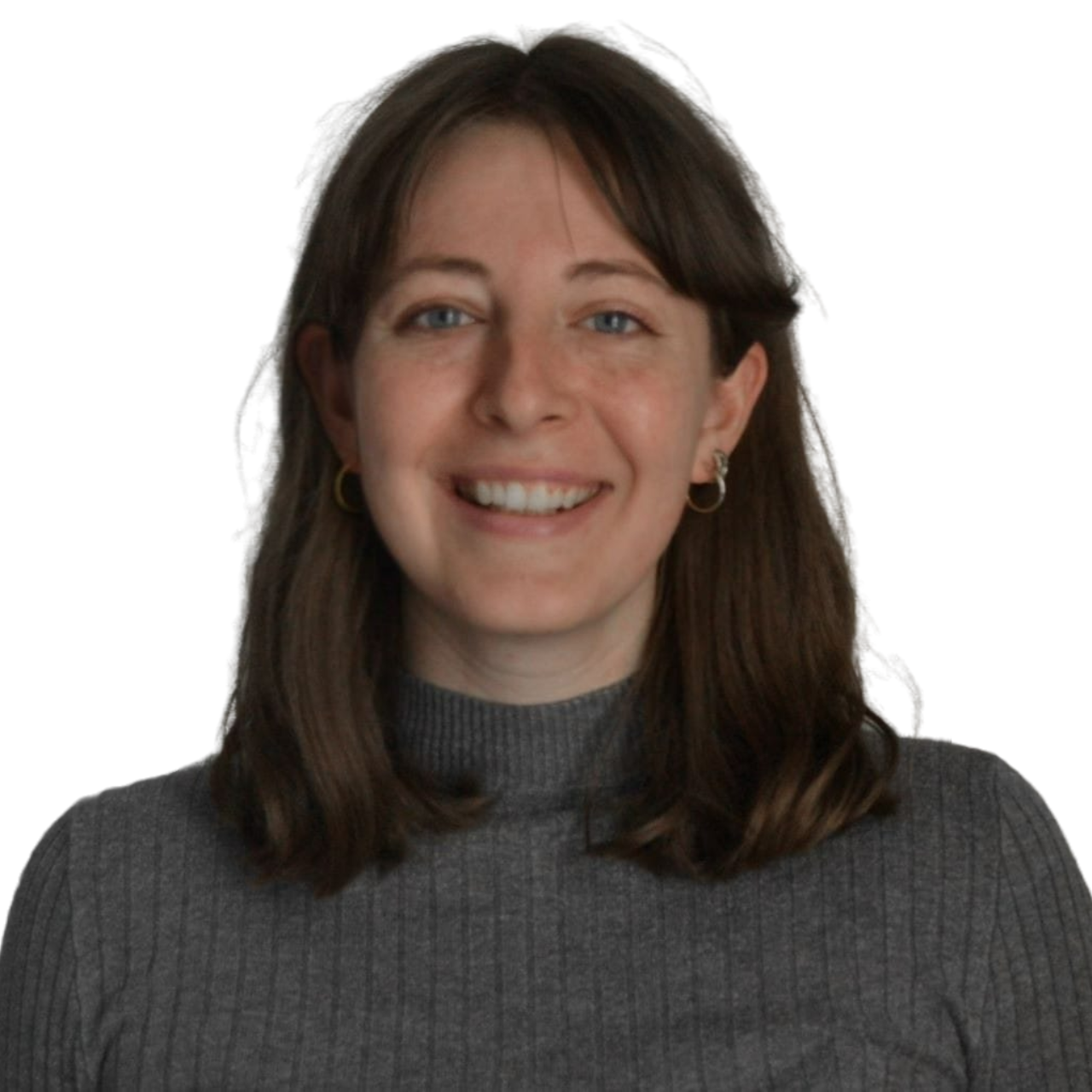